What’s the Limit with Simulation in Automotive? Hint: It’s not software
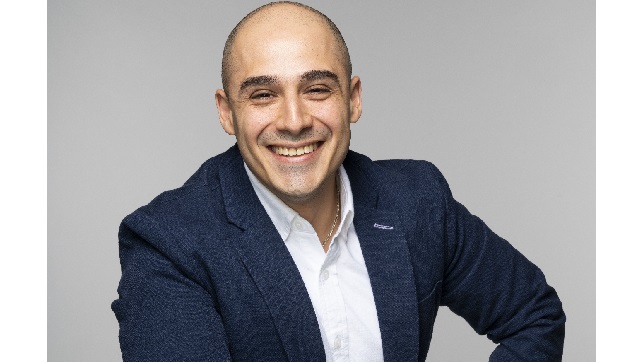
It’s hard to pin the single moment in which I had my first encounter with the automotive industry. From pictures, I know that my family’s car when I was born was an AMC Gremlin from the 70s which, by those day’s standards, was surprisingly equipped with an automatic transmission. Then I remember my mother’s favourite car, a 1994 V6 Cutlass Eurosport, with manual transmission, power windows, and fuel injection, with which I learned how to steer. My next big encounter, now as a driver, was with a 1990 Volkswagen Beetle, or as we call it in my country, Mexico, a Vocho. Each of those cars had innovations in their own way: their powertrains, the cooling systems, the number of electric elements and of course, they all represented an engineering challenge in their own times. Now, decades later that I think of them, I can appreciate the level of complexity that was met by the engineers involved, with the tools that they had at hand.
As a young engineer, my real encounter with the automotive industry was when I was trusted to help test engineers solve their challenges. I was a field engineer working with automotive OEMs and Tier 1 suppliers as part of my portfolio. The biggest one was a German car manufacturer with a massive development department that designed test equipment in-house. During that time, a lot of our conversations were about the equipment we would use, the test methodology, and the benefits of using the technology I was offering versus alternatives. There was a boom of embedded, reconfigurable devices and I recall them doing a lot of prototyping of their test systems. Fast iterations of many prototypes was a big value my solution delivered. Now, many years later, as my involvement with the automotive industry has changed, I find myself in more and more conversations that discuss the ability of technology to integrate and bring other tools onto one single software-connected toolchain that can span from design and simulation, to road test, with the objective of relating test requirements with test execution and results (Figure 1). The trend to maximize reuse, deliver on shorter timelines and do more test without increasing resources continues to consolidate in the automotive industry and as engineers, we recognize that without such connected approach, the risk of investing in specific tools that do the one job, but don’t provide value to future test stages, becomes too high to justify.
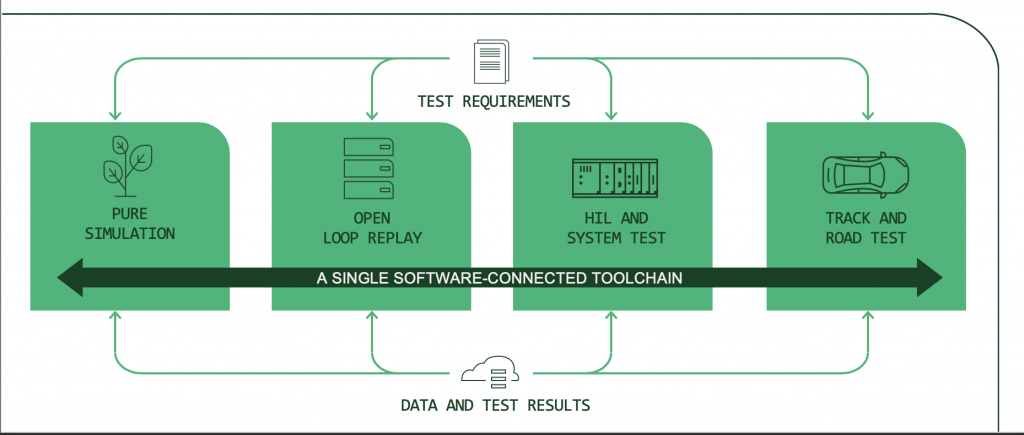
The ascent of simulation in automotive
Computer simulation technology started almost side-by-side with computers and, just as computers have evolved and improved drastically, simulation has grown to be used in almost all aspects of science and engineering with one major goal: to help predict what will happen to what we’re creating.
In automotive design, simulation is one of the drivers behind faster innovation, improved safety, and business sustainability. It allows you to “see” reality without creating it, to try designs without re-creating, to prototype without time-consuming hardware tasks, and to “finalize” without even starting. While there are multiple branches of simulation in automotive that we could explore, all the way from mechanical component design to vehicle dynamics, one of the most exciting −and critical− branches is in Advanced Driver Assistance Systems and Autonomous Driving (ADAS/AD).
To illustrate this criticality and the role of simulation, let’s use a simple example. You’re driving down the highway and there’s a piece of tire that ripped off from a truck. You can see it, you calculate distances, speeds, risks, and steer in a smooth curve to avoid the obstacle without even interfering with the lane next to you. Other drivers understand you’re not changing lanes, nobody overreacts, and off you all go.
Good, now consider this: have you ever encountered two of such pieces of tire in identical conditions in different occasions? I haven’t. I’ve encountered them in different weathers, times of day, positions, speeds, neighboring vehicles, and other conditions. Yet, I know what to do every time and I’m sure you do too. We know because, for some reason, we’re trained on how to manage such situation, either by experience or by observation. Cars are not trained and that’s where simulation comes in.
Simulation presents large benefits when designing and testing ADAS/AD systems and by far the single most important is supporting the development towards the safest possible end. Simulation opens the door to the car training facility that will accelerate the process within reasonable constraints, so that you can move on to the road test safely, confidently and effectively. Figure 2 below presents a few variables that change based on where the test is happening throughout the design and development process. Seeing words such as flexibility, liberty, efficiency, realism, dependency, is not surprising, but it should be enticing: how do we make that happen?
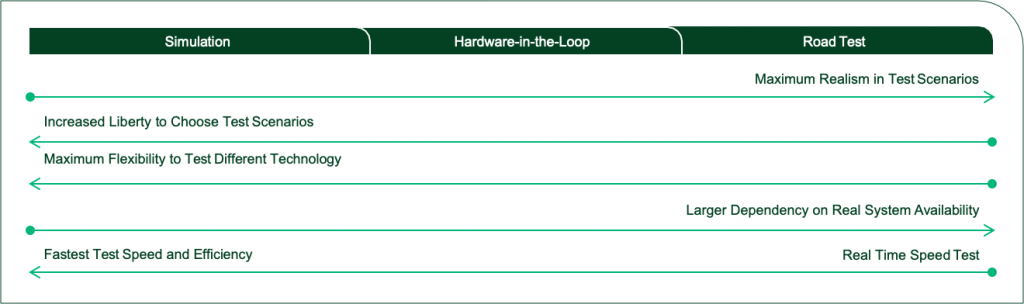
Companies such as Waymo rely on simulation and their “car”, which means essentially their driving algorithm, or Waymo Driver, go through billions of miles in simulation[1] before going on the road, with the intention that when it does go on the road, it’s as complete and safe as it can be and then improves upon itself with the real scenarios. At NI, we’ve seen companies at different starting points, anywhere from minimum leverage of simulation, to maximum use such as the Waymo example. Whatever that balance is at the moment, the trend is to move towards more simulation on design and test, especially for ADAS/AD components.
A couple months ago, Raghavendra Bhat, from ANSYS, wrote a valuable piece on automotive simulation around the topic of safety, security and reliability of autonomous vehicles in which he covered types of simulations, safety standards such as ISO 26262 and, in one of his closing paragraphs regarding how autonomous vehicles must be analysed to assess and resolve security risks, he makes this remark: “the vehicles must be continuously monitored for security exploitation throughout their lifetime, across the markets” [1]. Let the phrase to sink in and see how one word comes to mind: data.
The role of data in simulation
In figure 1, data is represented at the bottom of the illustration with connections to every stage of the test. That seamless flow of data across the stages also represents the purpose of making ADAS/AD systems as safe as they can be, and to accomplish it, several challenges and potential solutions can be assessed. Let’s drill one level down to look at the hardware-in-the-loop (HIL) type of test, abstracted in Figure 3.
Just like in the higher-level representation, data connects every stage and at the core, we have either a data centre that can be on-premise or a data cloud service. Simulation, in this example, is only one step in the HIL validation process but it cannot be seen in isolation.
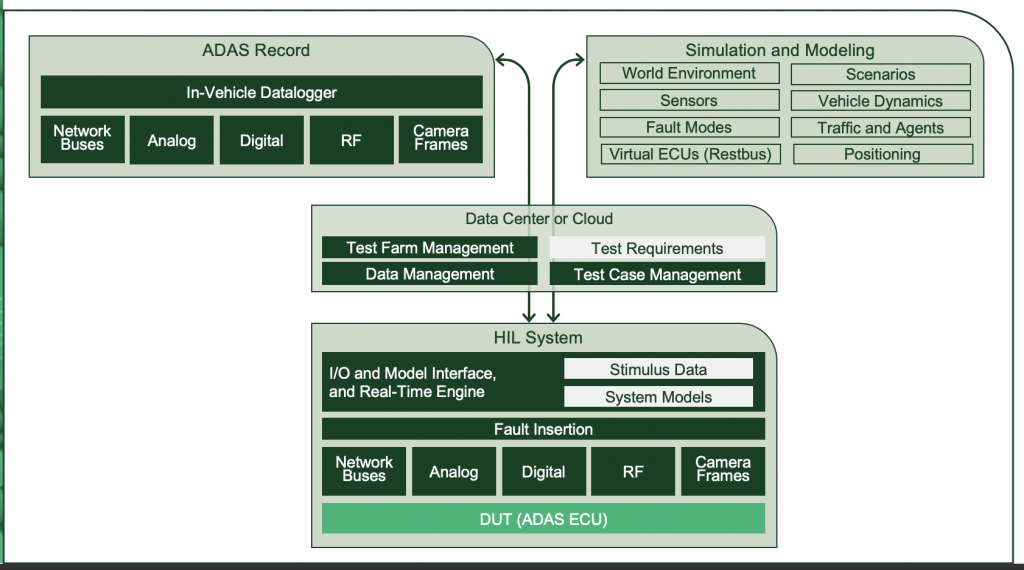
The role of simulation here goes beyond providing an environment with variables, standard and user-defined scenarios, customized configurations, and high-fidelity sensor data. It also has a very important role of providing data that represents all of those variables to a system that can send (play) it to the ADAS controller (ADAS ECU) you’re testing.
We know there are several tools for vehicle simulation in the market, each with their own strengths and areas of opportunities, but the one thing they have in common is precise data, and that common feature can become a differentiating factor when choosing the right tool for the task.
Let’s consider the example of simulating an Autonomous Emergency Braking (AEB) test scenario in which you have a car driving at a certain speed and encounters a vehicle stopped right in front. The simplest variables to modify are the speed and moment the brake command is sent, and with those two you already can have a large number of test cases to run. Now, let’s start adding complexity to the scenario: another sensor; for instance, a camera, to detect the same stopped car in a different way, a ramp of acceleration instead of constant speed, a slope on the road, different weather conditions, and you can go on and on adding complexity to the same AEB test scenario. Being able to effortlessly modify these variables is a minimum expectation when using simulation software. Being able to connect all the way, through data, to hardware that can eventually play the test scenario to the ADAS Controller is the area in which we see value.
Since that ADAS ECU will eventually go into a car, we have to test at many different phases. We have to send simulation data to the algorithm, we have to send raw sensor data to it, we have to send processed sensor data, we have to replay data previously recorded from real world scenarios, and we have to correlate all to test requirements, test plans and test results. Finally, we have to make sense of all that data so that the test engineers will have a clear view of what absolutely needs to be tested on the field/road, how, and with which level of completeness.
Make better use of simulation data, and data for simulation
Now that we’ve established the value and relative position of data within the test framework
let’s look at how we can make better use of it.
Better understanding of test coverage
Through a wider, multiangle, multi-process view of the test in all environments (simulation through road), data can confirm that the test is covered meets expectations and regulation and uncover areas that are not yet exhaustively explored. In other words, data should naturally become an input and an output of the simulation stage
Better simulation and statistical modelling
Simulation tool providers invest heavily in providing their users the ability of effortlessly configuring and defining scenarios that will be turned into the simulation data test engineers need. Their investment is not with the intention of including every single possible scenario, but to enable the user to explore their test scenarios to the maximum. Test data is a critical feedback loop to maximizing the value of scenario definition through statistical modelling and hence, the value of the simulation tool becomes proportional to the level of user-empowerment to define simulations that come from actual test results.
Test automation
For test case scenario generation, leveraging data from the automated process, it’s possible to eliminate unnecessary test re-runs and ensure the proper correlation of the test requirements with the test results.
Risk mitigation
Beyond the obvious benefit of having test result documentation to prevent recalls or failures, test data can drive decisions on capital investments, which reduces risks of going over-budget, over-time and over-working the test team.
Enable the future – AI and ML
Perhaps the most technically relevant element of data in test is how it opens the door to the future implementation of machine learning (ML), artificial intelligence (AI) and other technologies that will further test automation and bring simulation closer to reality more effectively.
In essence, proper leverage of data, enabled by the right simulation and test tools, unlocks the possibilities of faster test development and a shorter timeframe between the conception of safer, better tested ADAS technologies, to production and deployment in the cars we all use.
While compelling, the points regarding the value of data also uncover the limitations that still exists when performing test from simulation to production (Figure 4). When choosing how to do the simulation, we must ask ourselves if what we’re choosing serves the greater purpose of safest and most effective test down the line due to its interoperability, openness and interconnectedness.
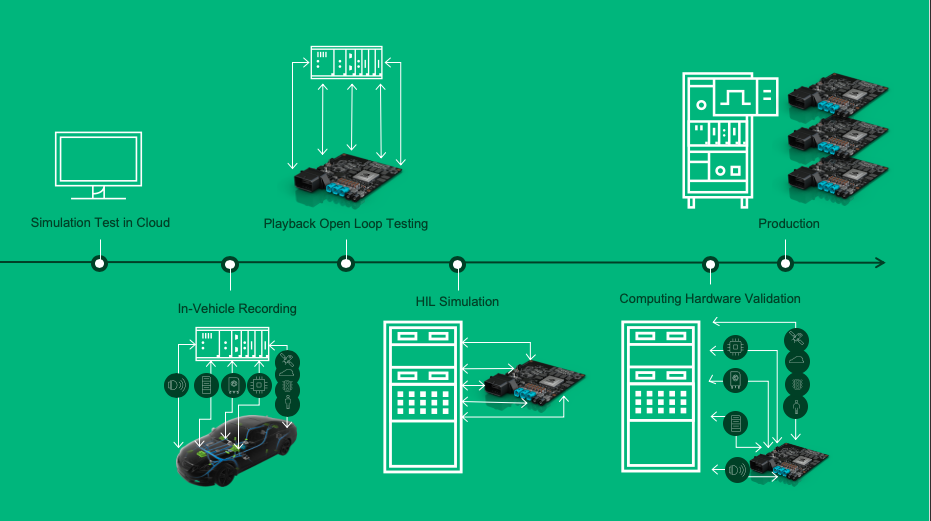
Conclusion
Throughout this article we’ve explored only a fraction of what simulation means to the automotive industry. This is not only because of how vast the topic is, but because, in the automotive test context, talking about simulation is really talking about data.
Early in the article I provided a few reference points of my experience with the automotive industry and how the innovation has been on par with the tools available. The designers of AMC did their best with the Gremlin over 5 decades ago. The creators of my Vocho did their best modelling of the airflow with the tools they had available at the time and decided on the design that, beyond some minor inconveniences, granted the car a level of simplicity and efficiency that was never matched again. Today, simulation allows us to virtually create and test anything we can think of without having to prototype it in the physical world first. With such powerful value, what’s limiting us? It’s the way we work with data from simulation, from test, from real world scenarios that’s limiting us. By not flowing freely amongst the test stages because of format limitations, by not being detached from the tool and attached to the process and by the level of competition it exists in providing “the best data platform”. When it’s time to choose our simulation and test tools, we should be compelled to think about how data from it will connect to the hardware we’ll later use for validation, and how it will relate test requirements with test result in the lab and on the road. While the “best data platform” comes to life, at NI we’ve worked with the right software-connected toolchain that works for you as the data bridge to take your test from simulation to road test, and from design to production, with transparency and openness, so data unleashes in the benefit of your design, and ultimately of the automotive industry.
Author:
Arturo Vargas Mercado
As Solutions Marketing Manager, Arturo is responsible for accelerating business within his prioritized focus area by using hisindustry and application expertise to position NI solutions to specific customers, at different stages of their solution-seeking journey.
Since becoming part of NI over 13 years ago, Arturo has held multiple, international roles in sales and marketing, complementing his experience in areas such as academic, energy, aerospace, automotive. Between 2014 and 2018 he was the marketing manager for Latin America, being responsible for the necessary strategic alignments between sales and marketing, and for ensuring the effectiveness of NI’s go-to-market plan for all geographies.
Published in Telematics Wire