Volvo Penta starts production of E-driveline for world’s first serial electric fire truck
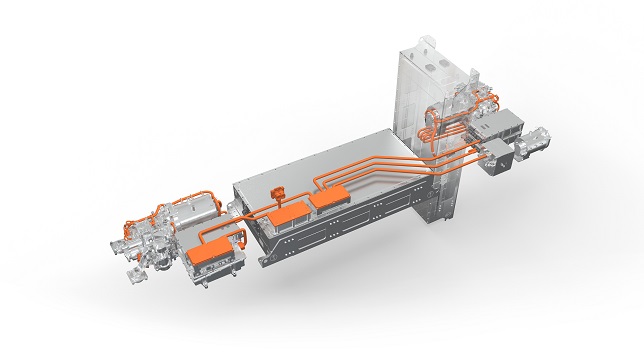
Volvo Penta has commenced production of bespoke electric drivelines for leading fire service vehicle manufacturer Rosenbauer’s pioneering fire truck, named “Revolutionary Technology” (RT).
“We announced our emob partnership with Rosenbauer in 2019, and we have gone from concept to start of production in record time,” says Giorgio Paris, President of Volvo Penta Industrial. “This is a milestone in our electrification journey. We see a growing demand for electric solutions in the market today and – through collaboration and pilot projects, such as this one – we aim to meet this demand and the expectations of the future.”
By adapting proven technology from Volvo Trucks and Volvo Buses,Volvo Penta and its customer Rosenbauer have introduced the world’s first electric fire truck, with a completely new vehicle architecture. This project is a true example of Volvo Penta’s customer-focused evolutionary approach.
Adapting & advancing
The RT pushed Volvo Penta’s electric drivelines to new heights. Unlike other Volvo Group EVs that might have two or sometimes three electric machines, the RT required four to do its job. All four electric machines have to be able to run simultaneously – two for propulsion, one for the range extender to provide extra battery power, and one for electric power takeoff, if fire-fighters want to rotate the foam pump for example. To achieve this, the Volvo Penta engineers created a system that is completely cutting edge in terms of Volvo Group technology.
Due to the required compact dimensions of a city fire truck, Volvo Penta created a new Active Cooling Unit (ACU). This component was developed in part collaboration with Rosenbauer. The new ACU draws on a 600V system – instead of the conventional 24V – this extra power allows Volvo Penta to not only cool the batteries but also offer cooling capacity to the Rosenbauer vehicle. This is one way Volvo Penta has optimized the design and adapted the complete electric driveline system for a specific vehicle, considering the exact application, usage, climate, and environment it will operate in.
Three Rosenbauer test firetrucks – powered by Volvo Penta electric drivelines – have already successfully been delivered to Berlin, Amsterdam, and Dubai. So far, the crews have been amazed at the RT’s battery capacity and the many other advantages of not having a large diesel engine – such as increase crew cabin space and more side panel storage.
Now the first electric drivelines have entered the production stage at the Volvo Penta Vara plant in Sweden. Here the ACU is manufactured, and the system is kitted – loaded with software and packed together – to make installation as straightforward as possible for the customer.
On a journey, together, with our customer
“When it comes to developing new technologies, like electromobility, we see our customers as our biggest asset,” says Giorgio. “We have developed strong working relationships with our customers over many years, which is key in the transformation towards more sustainable and new technology solutions. By working closely on different applications and in an array of sectors we can develop solutions – in a stepwise approach – that are reliable, safe, and create value, with the aim to bring an electromobility platform to our customers.”
Legislation and customer’s changing moral principles are driving a transition to more sustainable products. Volvo Penta has set firm climate commitments to support its customers in this transition. This switch from diesel-based technology to electrification is a key element in Volvo Penta’s transformation, alongside other new technological advancements.
“The RT’s success in real-world field tests and the start of production of the electric driveline are two milestones in Volvo Penta’s electrification journey,” concludes Giorgio. “A journey that will continue to be reinforced through strong collaboration. We will continue to perform and transform – focusing on today’s technology while at the same time further developing zero-emission solutions at an accelerated pace.”