Volkswagen plans to use 3D printing process in vehicle production
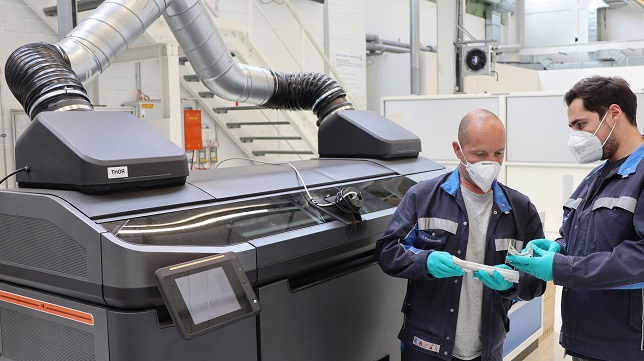
Volkswagen is pressing ahead with the use of innovative 3D printers in car production. For the first time, the newest process – known as binder jetting – is being used to manufacture components at the company’s main plant in Wolfsburg, Germany. Whereas conventional 3D printing uses a laser to build a component layer by layer from metallic powder, the binder jetting process uses an adhesive. The resulting metallic component is then heated and shaped. Using the binder jetting component reduces costs and increases productivity – for example, the components weigh only half as much as those made from sheet steel. Volkswagen is currently the only car maker using this 3D printing technology in the production process. “Despite the ongoing challenges of the coronavirus pandemic, we’re continuing to work on innovation,” says Christian Vollmer, member of the Board of Management of the Volkswagen Brand responsible for Production and Logistics. “Together with our partners, we aim to make 3D printing even more efficient in the years ahead and suitable for production-line use.”
Cedrik Neike, member of the Managing Board of Siemens AG and CEO Digital Industries: “We are very proud to support Volkswagen with our innovative 3D printing solutions. Our automation and software solutions are leading in industrial production applications. Using this technology, Volkswagen will be able to develop and produce components faster, more flexibly and using fewer resources.”
To achieve this innovative advance, Volkswagen has invested an amount in the mid-double-digit million euro range over the past five years. In addition, the company has entered into a software partnership with Siemens and expanded its existing collaboration with printer manufacturer HP Inc. With the first full-scale use of binder jetting, they intend to acquire important experience and learn, for example, which components can be produced economically and quickly in the future or how additive manufacturing can support the digital transformation of production at Volkswagen.
HP is providing the high-tech printers needed and Siemens the special software for additive manufacturing. One key process step that has been worked on jointly by Siemens and VW is optimizing the positioning of components in the build chamber. Known as nesting, this technique makes it possible to produce twice as many parts per print session.
From summer, the three companies intend to establish a joint expert team at the high-tech 3D printing center which opened in Wolfsburg at the end of 2018 and enables the manufacture of complex automotive components using 3D printing. The center also trains employees in the use of these technologies.
By 2025, the aim is to produce up to 100,000 components by 3D printing in Wolfsburg each year. The first components made using the binder jetting process have gone to Osnabrück for certification: components for the A pillar of the T-Roc convertible. These weigh almost 50 percent less than conventional components made from sheet steel. This reduction alone makes the process especially interesting for automotive production applications. Volkswagen has already successfully conducted crash tests on 3D-printed metallic vehicle components. Until now, the production of larger volumes was not cost-effective enough. However, the new technology and the collaboration will now make production-line use economically viable.
More than one million components printed in 25 years
Volkswagen has been using 3D printing for 25 years, starting in Technical Development with the goal of accelerating vehicle development and reducing costs. Today, there are 13 units at the Wolfsburg plant using various printing processes to manufacture both plastic and metal components. Typical examples are plastic components for prototypes such as center consoles, door cladding, instrument panels and bumpers. Printed metal components include intake manifolds, radiators, brackets and support elements. Over the past 25 years, more than one million components have been produced.
Volkswagen’s collaboration with Siemens is part of a comprehensive strategic partnership in the field of digital production platforms. Volkswagen Board of Management member Vollmer: “I’m pleased that we have a strong and innovative partner in Siemens so we can start working on the car production processes of the future. The example of 3D printing shows that this transformation harbors many diverse opportunities for innovation.”
One Comment