Recyclable materials for cars with additive specialties from Evonik
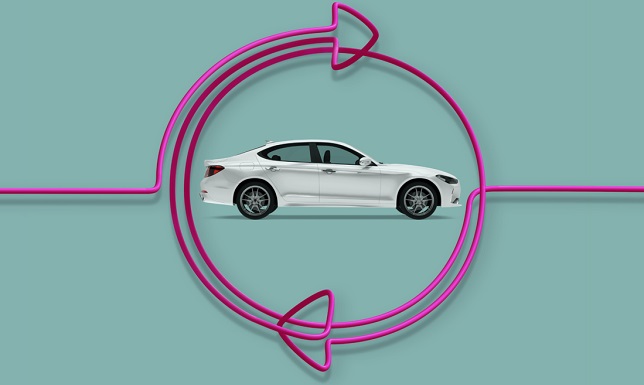
A consortium of 19 leading industrial companies and research institutes, including the BMW Group, Evonik, Thyssenkrupp, the Fraunhofer Institute, and the Technical University of Munich, has set itself the goal of developing new processes for using sustainable materials for circular automotive production. Evonik is contributing its expertise in plastics and additives for recycling to the project. The project, which is funded for three years by the German Federal Ministry of Economics and Climate Protection (BMWK), was launched at the end of last year.
The core of the “Future Sustainable Car Materials (FSCM)” initiative launched by BMW is to develop innovative process routes and material concepts for large parts of the value chain, thus enabling a circular economy in vehicle production.
“We are pleased to contribute our specialty chemicals expertise to this pioneering consortium of industry leaders and internationally renowned research institutions to develop circular plastics solutions for the automobiles of tomorrow,” said Lauren Kjeldsen, member of the Executive Board of Evonik Operations GmbH and head of the Smart Materials Division.
According to the principle of the circular economy, materials must be kept in the value chain after they have reached the end of their useful life so that new objects, such as automotive parts, can be produced without the use of fossil resources. It is particularly challenging to keep these materials in the cycle while maintaining the same quality and safety properties.
“Our mechanical recycling experts work closely with recyclers to prepare methods for cleaning up plastic parts, such as separating paint at the end of useful life,” said Patrick Glöckner, Head of the Global Circular Plastics Program at Evonik. “We also work with compounders to develop solutions for using the highest possible proportion of recycled plastics in new automotive parts.”
This form of integrated collaboration enables the consortium to quickly identify challenges and jointly develop solutions. Due to the high complexity of automotive manufacturing, the participants in the FSCM project are optimistic that the knowledge gained can also be applied to other industrial products in the future, such as commercial vehicles, electrical and household appliances, and will thus be a decisive impetus for future circular economy systems in the German economy.