Range Controversy: A Vehicle Data Monetization Opportunity
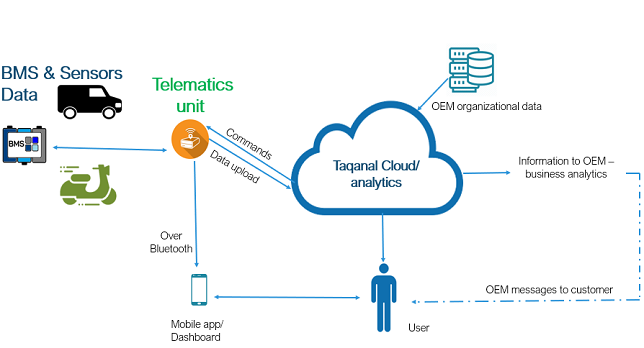
The TATA Nexon EV “Range” controversy has been a topic of hot debates in recent times. ARAI certified the “range” of the vehicle as 312 Kms. However, a customer sued TATA Motors because he did not get the claimed range. Several other customers joined the chorus. The Delhi government delisted it from its subsidy scheme, and court provided interim relief.
Accuracy of prediction of “range” is not such a big deal in ICE (Internal Combustion Engines; such as Petrol/Diesel engines) vehicles due to ubiquitous presence of gas stations. However, a vehicle with better fuel economy is more desirable. In case of EVs, customer expectation about “Predicted Range” accuracy is higher. “Higher Range ” requires bigger batteries, increasing the cost of the vehicle. Batteries constitute more than 50% of the cost of an EV. Having paid more, just for a bigger range, customer expectations around accuracy of “range claim” are higher.
The controversy around TATA Nexon EV’s range arose due to customer perception of the OEM’s claim of range
Is it so difficult to accurately estimate the remaining range?
Good solutions are available, but they require instrumentation & computing. All these solutions, work on the basic principle of measuring the amount of fuel left in the tank (or charge in the battery in case of an EV), and estimating the distance the vehicle can go on that fuel.
Fairly accurate measurements of fuel in the tank, average fuel consumption, and current fuel consumption have been available in mid-range ICE vehicles for a while. Also, as gas stations are ubiquitous, there is less anxiety about “how much will my vehicle go in reserve”.
However, he problem of estimating range in EVs is fairly complex:
- Estimating the “Remaining Useful Charge” in the Battery is often done using estimating the “State of Charge (SoC)”. Estimating SoC accurately is a known challenge.
- Range estimate at any moment depends on current load, ambient temp., route (elevation, road/conditions), wind-direction/speed,…), time of the day, driving mode & style…
Estimating Useful Range/Soc Accurately
Modern BMS’s (the Battery Management System inside batteries that controls, charging/discharging of the battery, monitors all key parameters, and performs operations to keep the battery in an optimum state of safety, and operation) maintain an estimate of SoC. The algorithms that estimate SoC have been growing in sophistication, and estimation accuracy. For higher accuracy, the algorithms need detailed historical data.
However, due to memory & compute limitations on the BMS, it is not possible to keep large amount of historical data, and process them. This limitation is overcome, by sending all the data collected in the BMS to a “Cloud” (a remotely accessible infrastructure where large amount of data can be stored, and vast computations can be done economically. In the Cloud, incoming data from the BMS, and past data is continuously analyzed. Typically, a very large number of batteries send their data individually to the cloud, and similar algorithms work on data coming from each, and every battery. The Machine-Learning based models in the cloud continuously fine-tune their algorithms for determining the SoC for each battery. With knowledge of history of each battery, and that of a large number of other batteries, the SoC accuracy for each battery improves significantly. Like all Machine Learning applications, the SoC estimation accuracy improves with the amount of historical data from a large number of connected batteries.
As these computations are done in the cloud, where memory, and CPU resources are not a constraint, the SoC estimation accuracy is significantly higher, and keeps improving with time. Typically, the current estimate is sent to the battery at regular intervals, ensuring an accurate estimate of the remaining charge in the battery is available at all times.
Battery is the most expensive part in any EV. To keep costs low, many a times, they are not instrumented well enough. Worse, a lot of times, there is no way to find out the goings on inside a battery; there is no way to communicate with the battery. Poor instrumentation, lack of visibility, inability to get sufficient data, and process it not only inhibits accurate SoC, it also results in compromised safety, reliability, and long-term TCO (Total Cost of Ownership).
In the past, the engine was given a divine status: auto-owners were preached to offer the most expensive “synthetic motor oil” to the presiding deity in the vehicle with religious punctuality. In an EV, the battery rightfully deserves the status equal to or better than an engine in an ICE vehicle.
Typically, cloud-connected vehicles do much more than just SoC/Remaining Range estimation. All the measured data is continuously analysed to predict any failures, and preventive maintenance is advised to eliminate breakdowns. Some of the data & analytics are used by the OEM, some by the service stations, some by the parts/sub-system makers, some by law-enforcement, some by neighbouring vehicles, some by insurance companies… The following sketch depicts the general use case:
Remaining Range estimation at any moment
“Remaining Range” depends on a lot of factors that change dynamically: Load, Road conditions, wind-speed, wind-direction, ambient temperature, elevation, time-of-the day, driving-speed, and driving style.
Larger the number of passengers or payload, larger will be the energy consumption. Bad roads cause more friction, and more energy is consumed traveling on those. If the wind is favorable, and blowing in the direction of the vehicle, less energy will be consumed. Batteries have different behaviors at different temperatures. Climbing to a hill station can consume significantly more energy (while coming down can generate energy in an EV, and charge the batteries). Time of the day makes a difference too: Headlights consume energy during dark conditions & temperature varies during the day. Driving in economy modes can return significantly higher mileage than driving in Sports mode. Energy for all loads (AC, heating, lighting, wipers, infotainment, ADAS…) comes from the battery, and affects the range.
All the parameters affecting energy consumptions need to be measured at frequent intervals. A vehicle going at 60KMPH covers a distance of 16.67 Kms every second. Some of the parameters above (such as road conditions, elevation) can change during that interval. Ideally, the sampling rate should increase with increasing speed.
Cost-effective sensors are available to measure most of the parameters. Instrumentation in vehicles has already been increasing to introduce ADAS. Algorithms are available to use all the measurements, and refine the estimate of current & projected energy consumption. Combining it with an accurate estimate of SoC at the moment, it is easy to provide an accurate estimate of range.
Summary
Range” is dynamic. It changes with current load, ambient temp., route (elevation, road/conditions), wind-direction/speed…), time of the day, driving mode & style…Technology exists to predict range accurately, at every moment in an EV. It changes, if conditions change. The fuel consumption/range estimation in an ICE engine vehicle is far more error prone, as they consume fuel while idling too. EVs (unless using AC/Lights) don’t use any energy while stopped. People don’t complain about poor range prediction in ICE vehicles due to ubiquity of gas stations. Absence of fast charging stations makes “Accurate Range Prediction” a necessity in EVs.
With a well instrumented, cloud-connected battery, instrumentation in the vehicle, and a combination of cloud-computing, and on-boarding computing it is possible to estimate “Remaining Range” with a very high degree of accuracy. As OEMs introduce ADAS related features, sensors needed to measure parameters needed for these computations are likely to become standard. Algorithms already exist. EV OEMs should consider making their customers happy with the “Accurate Remaining Range” feature.
Author:
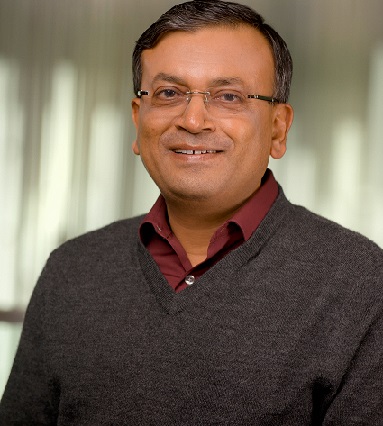
Mohan Satyaranjan
CEO
Taqanal Energy
Mohan Satyaranjan is currently an entrepreneur focused on developing technology to address barriers to EV adoption. He is CEO@Taqanal Energy, a company innovating in the area of “Cloud Connected Energy Storage Systems”. Prior to turning an entrepreneur, Mohan spent more than 35 years in Networking & Telecom R&D. He built ‘billion+ dollars a year’ product lines, from scratch, at both Cisco Systems, and Juniper Networks. He has held director, and above positions at NetApp, Juniper Networks, and Cisco Systems. At Motorola he played a significant role in developing the world’s first GPRS capable subscriber device.
Published in Telematics Wire