Predictive Maintenance: Audi Maintenance uses data to predict the future
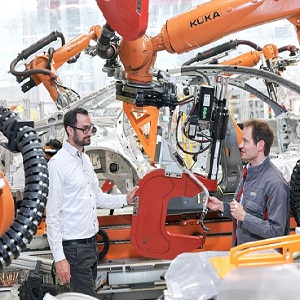
Smart, digital maintenance: The “Predictive Maintenance” project at the Audi Neckarsulm site makes maintaining production equipment more efficient and reduces production downtime. Maintenance experts collect and interpret associated data and can predict wear on production equipment.
The Group-wide pioneering project is being tested in the body shop at the Neckarsulm site. “Predictive Maintenance” detects possible wear on a riveting machine that joins various body components. “The punch riveting systems drive between 600,000 and 1.2 million rivets through a plastic tube using compressed air. This technology propels the punch rivet through the tube at up to 20 meters per second. This results in traces of wear inside the tube,” says Andreas Rieker, maintenance planner at the Audi Neckarsulm site.
To determine the best time to replace the tubes, the Audi staff used big data to collect and analyze over a million pieces of data. Unexpected equipment failures can be minimized as a result and associated maintenance work carried out in production-free periods. “Our aim is to detect wear and emerging problems before they happen. We look into the future so to speak – with the aid of data, algorithms and measured values,” says Mathias Mayer from the Data Driven Production Tech Hub at the Audi Neckarsulm site.
Employees are also standardizing processes to connect multiple pieces of equipment and machinery to databases. In the near future, other process data will also be read out and interpreted. This will make the job of the maintenance personnel easier and make production more efficient. “Predictive Maintenance” is due to enter series production following a successful pilot phase. It is also due to be used on other equipment and in other areas.
The “iMaintenance” app also assists the maintenance personnel in the Neckarsulm body shop. The app is based on a knowledge database with around 5,000 pages of material, clear troubleshooting measures and recommended action. If a machine reports an error code, the Audi employee can simply enter the relevant code on their tablet to access step-by-step instructions on how to remedy the fault. The “iMaintenance” app is part of the “Mobile Integrated Maintenance” joint project between the Audi Ingolstadt and Neckarsulm sites. This joint project includes other innovative projects, such as the “Audi Mobile Maintenance” app.