Optimizing xEV power electronics design through advanced simulations
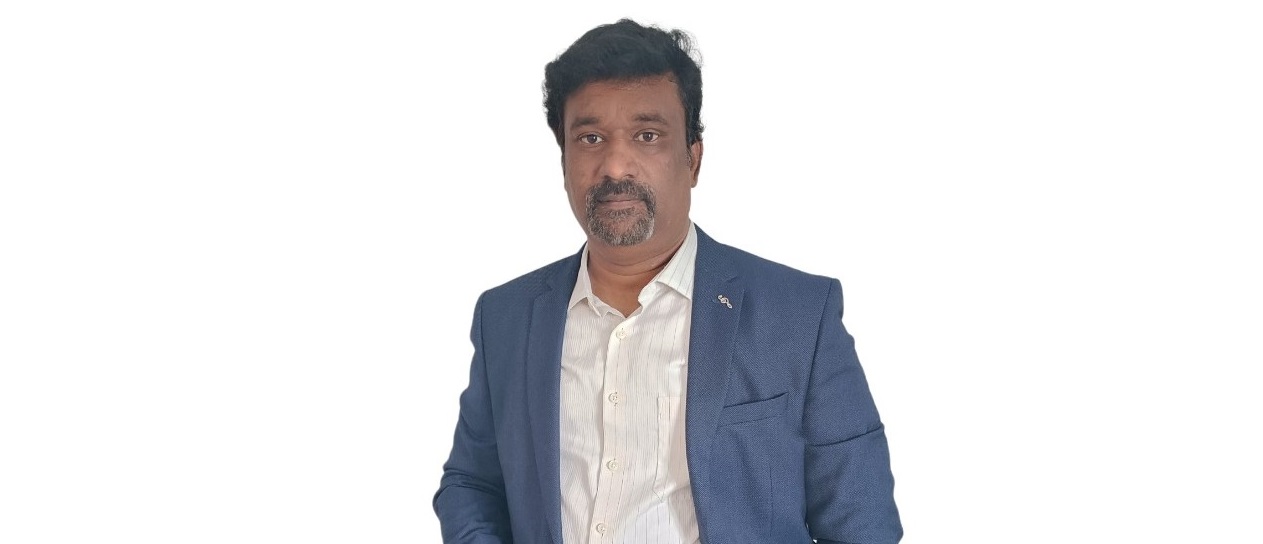
Telematics Wire in discussion with Perumal AT, Head – Electrification CoE, EV/FCV – Mechanical & Electromechanical Design, Tata Elxsi, explores optimising xEV power electronics design through advanced simulations.
Can you elaborate more on xEV Power Electronics Design?
The electric vehicle market today is on the rise and will continue to boom in the coming years. When we speak of power electronics design in xEVs, it covers a wide range of factors like the design of the electronic systems, controls of the electrical energy within the vehicle and so on. Power electronics technology is crucial as it converts and controls electrical energy between vehicle batteries, motors, and other components.
Power electronics are involved in the design of charging systems, power conversion and management systems, and energy management systems, especially since there’s a shift from low-voltage to high-voltage components. At the same time, a Battery Management System or BMS is a crucial part of xEV power electronics. This system monitors and manages the health, state of charge, and state of health of the vehicle’s battery by ensuring its safe and optimal operation. This also brings us to thermal design which includes heat sinks, cooling systems and other technologies that ensure the vehicle keeps running at an optimal temperature and manages the heat generated by power electronics components.
In short, power electronics design in xEVs is multidisciplinary and combines various fields like thermal management, control systems, electronic design, electrical engineering and more. The end result is an efficient, reliable and optimized power system for electric vehicles that maximizes range and meets the demands of automotive applications.
How can advanced simulations be leveraged to accelerate this, especially when compared with traditional test-fail-fix approach?
Today, we are inching closer towards electric and autonomous mobility. Modern vehicles are highly complex and come with added electronic components that cater to the demand for increased power. The need for reliable power electronics is of paramount importance, especially with advanced simulations as it helps reduce product development time and cost. For instance, many OEMs have begun developing their own high-voltage platforms. Here are a few more instances –
Inverter/Converter Design: Inverters are used to convert direct current (DC) from the vehicle’s battery into alternating current (AC) for the electric motor. At the same time, converters are employed to transform the voltage level of electrical power within the vehicle. DC-DC converters, for example, may be used to adjust the voltage from the battery to match the requirements of various vehicle components.
Transient Analysis: Advanced simulations can model and analyze the dynamic behavior of power electronics systems during transients, enabling engineers to optimize control strategies for fast-changing conditions, such as acceleration and deceleration.
Design Optimization: Simulations for power electronics allow engineers to access several design parameters faster and more efficiently, which further allows them to check the performance of components like inverters, converters and so on. At the same time, advanced simulations enable the testing of different circuit topologies and configurations to identify the most efficient and cost-effective solutions.
Thermal Analysis: Advanced simulations play a key role in predicting and managing heat dissipation in power electronics components. This is crucial for designing effective thermal management systems, while also ensuring the reliability and longevity of the components. Simulations can also model the performance of cooling systems, providing resources to optimize heat exchanger designs and fan configurations for efficient thermal control.
System Integration: In modern industry, virtual prototyping plays a crucial role. Simulations enable engineers to seamlessly integrate power electronics components into the complete vehicle system and evaluate their interactions with other subsystems prior to the creation of physical prototypes.
Machine Learning Integration: These advanced simulations can be combined with machine learning techniques to optimize control algorithms for power electronics systems. This iterative process can lead to improved performance and efficiency in the long run.
Simply put, simulations enable a thorough understanding of system behaviour, allowing for rapid prototyping, optimization, and the identification of potential issues before physical prototypes are built and tested. This iterative and virtual approach accelerates the development process and contributes to the overall advancement of electric vehicle technology.
What are some of the challenges faced by OEMs when it comes to simulations for EVs?
Every day, new technologies emerge, offering fresh advantages for OEMs. Nevertheless, OEMs encounter several challenges in the simulation process for EVs. Acquiring and integrating advanced simulations can be costly, making it a hurdle for OEMs to maintain a competitive edge. Here are some challenges OEMs face:
Complex System Integration: When it comes to EVs, several subsystems like power electronics, thermal management, controls, and mechanical components are involved. Simulating the interactions between these diverse systems can be complex and challenging.
Accuracy of Models: Ensuring that simulation models accurately represent real-world behaviour is another significant challenge that many OEMs face. Models need to be validated against physical test data, and uncertainties in parameters can affect the accuracy of predictions.
Real-World Challenges: This brings us to another prominent challenge that many OEMs face, which is real-world variability. Simulating the impact of real-world variability includes varying environmental conditions like temperature, humidity, and road conditions. These can affect the performance of EVs, and accurately representing these in simulations is complex.
Battery Modelling: Modeling the behaviour of advanced battery systems accurately is challenging due to the complex electrochemical processes, thermal effects, and ageing mechanisms. Developing accurate battery models is crucial for predicting range and battery life.
Regulatory Compliances: Meeting regulatory standards and certifications often requires extensive testing, where simulations need to align with testing protocols and standards. This further needs to ensure that the virtual testing process is accepted by regulatory bodies, which can be quite challenging for OEMs.
Addressing Human Factor: More importantly, simulating the interaction between electric vehicles and human drivers, especially in the context of advanced driver assistance systems (ADAS), involves complex human behaviour modelling. This adds an additional layer of difficulty to simulations.
One of the ways to overcome these challenges is through continuous collaboration across industries. This increases the efforts to standardize simulation practices and address the challenges to enhance accuracy, efficiency, and reliability.
In what ways can simulations be applied to predict the reliability of power electronic systems, encompassing areas such as solder fatigue, random vibrations, mechanical shock, and thermal analysis?
Simulations play a crucial role in predicting the reliability of power electronic systems, offering insights into various stress factors such as solder fatigue, random vibrations, mechanical shock, and thermal analysis. Here are ways simulations can be applied in these areas:
1) Solder Fatigue Analysis:
Finite Element Analysis (FEA): Simulations can be used to model the thermal cycling and mechanical loading experienced by solder joints in power electronic devices. FEA helps analyze the stress distribution in the solder joints, predicting areas prone to fatigue failure.
Thermal Cycling Simulations: By modeling the temperature variations during device operation and power cycling, simulations can estimate the number of thermal cycles and predict the solder joint fatigue life.
2) Random Vibrations:
Modal Analysis: Simulations can be employed to perform modal analysis to understand the natural frequencies and mode shapes of the power electronic system. Random vibration simulations can then be carried out to assess the response of the system to various vibration frequencies and amplitudes.
Shock Response Spectrum (SRS) Analysis: Simulations can predict how power electronic systems respond to mechanical shocks by analyzing their behavior under different shock profiles, helping to identify weak points and potential failure modes.
3) Mechanical Shock Analysis:
Drop and Impact Simulations: Using FEA, simulations can replicate real-world mechanical shock scenarios, such as drop and impact tests. This helps assess the structural integrity of the power electronic components and identify potential weak points.
Material Strength Analysis: Simulations can predict the stress and strain distribution in materials subjected to mechanical shock, aiding in the design and selection of materials with appropriate mechanical properties.
4) Thermal Analysis:
Computational Fluid Dynamics (CFD): CFD simulations can model the heat transfer within power electronic devices, predicting temperature distributions and identifying hotspots. This information is crucial for assessing the thermal performance and reliability of the system.
Transient Thermal Analysis: Simulations can predict how power electronic systems respond to transient thermal events, such as power surges or rapid changes in load. This helps in evaluating the thermal management system’s effectiveness and preventing overheating.
5) Integrated Simulations:
Multiphysics Simulations: Combining multiple physics simulations, such as coupling thermal analysis with structural analysis, provides a more realistic representation of the interactions between different stress factors. This integrated approach enhances the accuracy of reliability predictions.
6) Statistical Methods:
Monte Carlo Simulations: These simulations can be used to assess the reliability of power electronic systems under uncertain conditions by considering variations in parameters, such as material properties or environmental conditions.
Applying these simulation techniques provides a comprehensive understanding of the reliability of power electronic systems, allowing for informed design decisions and optimizations to enhance overall system performance and longevity.
Insights on the current trends and industry best practices when it comes to testing and optimizing power electronic systems and subsystems for xEVs
The EV industry is a dynamic one that is rapidly changing with trends and industry-best practices shaping the testing and optimization of power electronic systems. Here are some of the industry trends and practices of power electronics –
Collaboration and Standardization: One of the dominant trends we have been seeing is a collaboration between OEMs, suppliers, and industry stakeholders to establish standards for power electronic components. This further ensures interoperability and facilitates a more streamlined development process.
Test Automation: Another industry practice that has been consistent and will continue for years to come is implementing test automation. This helps OEMs improve testing efficiency, reduce human error, and accelerate the testing and validation phase of power electronic systems.
Lifecycle Analysis: Similarly, conducting lifecycle analysis to understand the environmental impact of power electronic systems has been another predominant trend. At the same time, making design decisions that align with sustainability goals has been quite impactful for OEMs.
Advanced Simulation and Modeling: The use of advanced simulation tools, such as SPICE-based simulations and multiphysics simulations is another key trend. This helps in modelling and optimizing power electronic systems before physical prototyping.
Integrated Design Approach: Another industry practice is bringing a shift towards integrated design approaches. This includes the entire powertrain system, including power electronics, electric motor, and battery, to optimize overall efficiency and performance.
Cybersecurity: Advanced cybersecurity is the need of the hour across industries and verticals. Integration of cybersecurity measures in power electronic systems to protect against potential cyber threats and ensure the safety and security of xEVs is another important trend to witness.
Digital Twins: OEMs will continue to tap into digital twin technology. This will help in creating virtual replicas of power electronic systems, enabling real-time monitoring, diagnostics, and predictive maintenance.
About Perumal AT: He is Head – Electrification CoE, EV/FCV – Mechanical & Electromechanical Design, Tata Elxsi. Prior to joining Tata Elxsi he was working with Tata Motors as Design Engineer.