Mindsphere app Predictive Service Assistance uses AI to optimize maintenance efficiency of drive systems
Early detection of anomalies in the drivetrain with the support of artificial intelligence
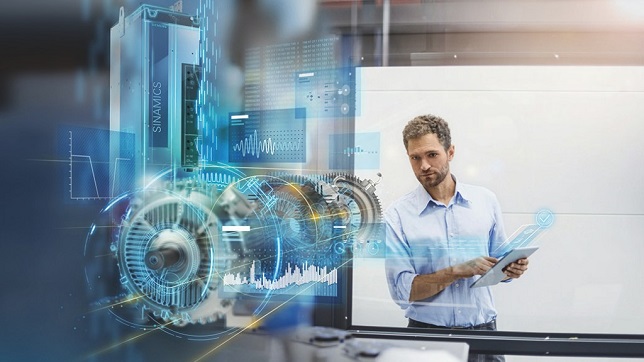
Siemens has supplemented the Mindsphere application Predictive Service Assistance with an AI-based module. The new Artificial Intelligence module identifies concrete fault patterns in motors at an early stage, such as misalignment or a defective bearing. The application thus helps users to reduce downtimes and further improve spare parts and maintenance processes. The new Artificial Intelligence module for motors uses a neural network to solve what was previously implemented using a defined KPI limit value. This enables the module to detect anomalies even before the defined limit value and provides clear indications of the type and severity of faults and their development. As soon as the application detects signs of an error, it warns the user and generates a due date that indicates when the error should ideally be corrected and what corrective action is recommended to prevent an unplanned downtime. Predictive Service Assistance with the new AI-based Artificial Intelligence module is offered as part of a Predictive Service Assessment.
The Mindsphere application Predictive Service Assistance is a central element of Predictive Services for Drive Systems, a standardized extension to the local service contract. It is used for more efficient maintenance of Sinamics and Simotics drive systems used on pumps, fans, and compressors, among other things. With Predictive Services for Drive Systems, customers benefit from higher productivity and reduced unplanned downtime of their machines and systems. With the support of the respective Mindsphere application, users also enjoy full transparency on spare parts and maintenance activities to minimize risks through simple weak-point analysis. The application also contributes to more efficient maintenance and reduced planned downtimes.