How much fuel is really in your tank?
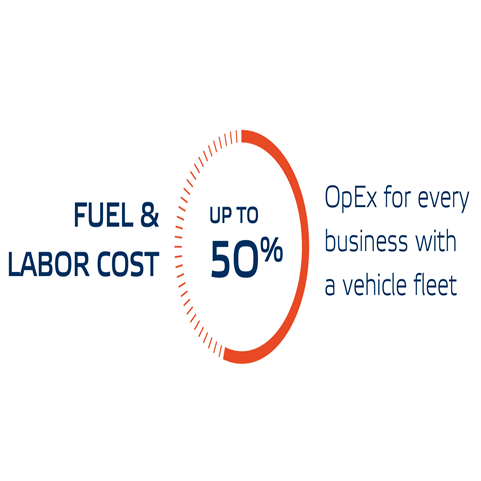
It’s no surprise to any fleet owner to learn that fuel is a massive operational expense. Fuel and labor can constitute up to 50% of operational spend for any business with a vehicle fleet*, so managing fuel effectively is critical. 49% of companies that implement fleet monitoring solutions report fuel savings as a benefit, ** and companies save 20-25% on average on fuel with a fleet monitoring solution in place. ***
Businesses need accurate fuel monitoring to minimize inefficient driving, vehicle idling, fuel wastage and fraud. But which technology is best?
Fuel Consumption vs Fuel Level
The difference between fuel consumption and fuel levels is very important. Fuel consumption data tells you how far a vehicle goes on a liter of fuel. However, only fuel level data can help you detect inefficient fuel usage and fraud.
Top Industry Technologies
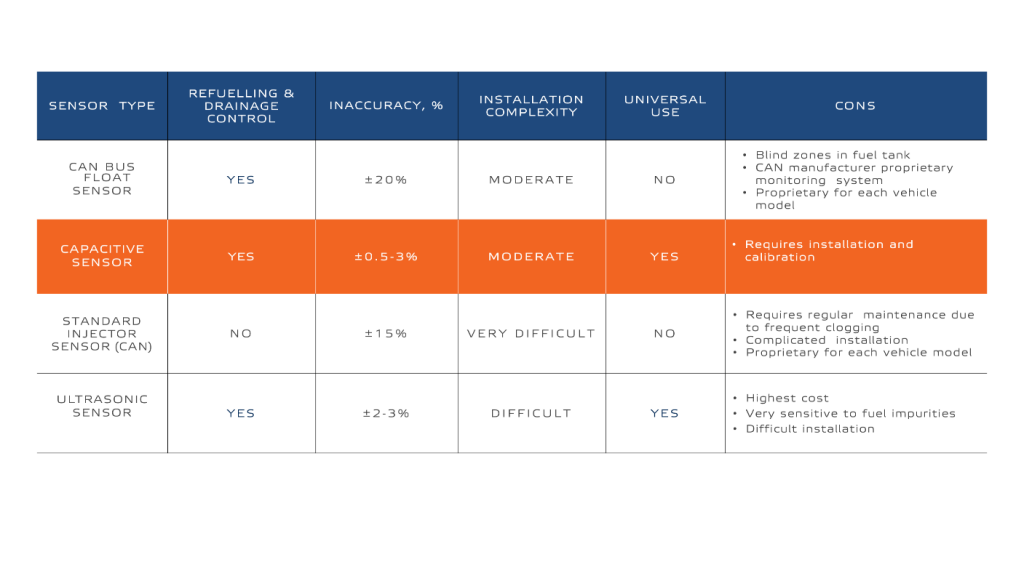
*Frost & Sullivan, Future of Logistics, 13 September 2016
**Fleet Answers, Telematics Survey: Industry Insights in 2017, Fall 2017
***Frost & Sullivan, Future of Logistics, 13 September 2016
Let’s take a look at a few leading fuel measurement technologies.
CAN bus sensors
There are two types of these popular devices.
CAN bus injector sensors deliver information about fuel injection into the engine cylinders. They assess consumption while driving. CAN bus float sensors combine a float and float value switch in the form of a variable resistor. They evaluate how full the fuel tank is.
Some fleet operators use both to create an enhanced measurement system. CAN bus sensors cannot be installed on vehicles manufactured before 2000 and certain special transport vehicles.
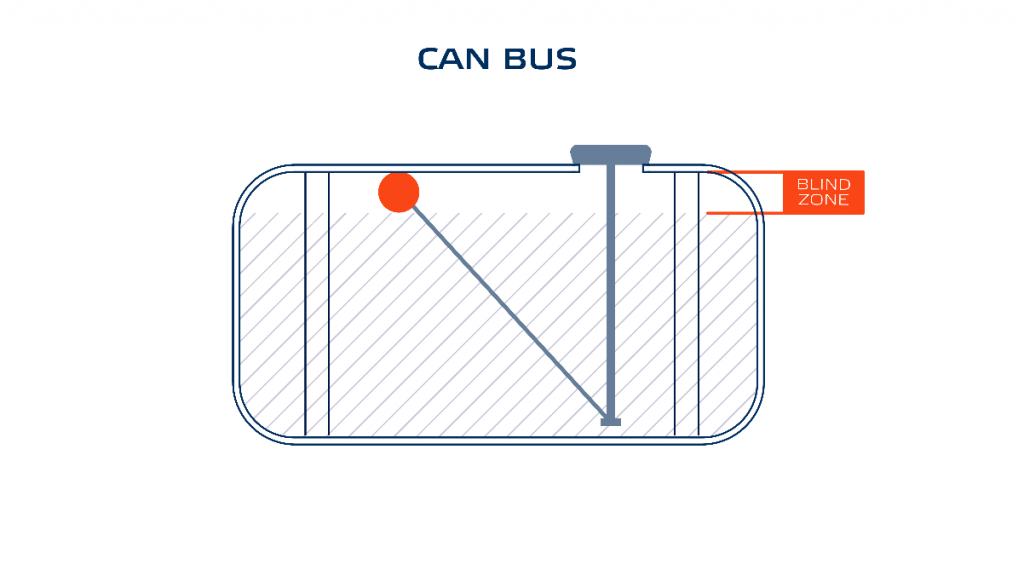
CAN bus injector sensor
Advantages:
- Delivers information in real time. Easy to connect.
Disadvantages:
- Does not measure fuel level; cannot recognize draining and refueling.
- Only reliable in new or near-new vehicles traveling along good-quality roads over flat terrain.
- Steady traffic speed enables accuracy. Complex driving conditions cause errors to accumulate.
- Accuracy is undermined by driving style, fuel equipment and injection nozzle quality, fuel line and atmospheric pressure, air strainer quality and fuel viscosity.
CAN bus floating sensor
Advantages:
- Indicates when it is time to refuel. Easy to connect.
Disadvantages:
- Blind zones representing up to 10% of volume at the top and a further 10% at the bottom of the fuel tank, causing inaccuracy of up to 20%.
- Requires calibration of tank to get information in liters.
- Variable resistor can suffer damage that makes it lose contact, distorting the signal.
- Variable resistor has just 30 divisions, so accuracy cannot be better than ±3% of the total volume. For instance, in a 700-liter tank the value of one division will be ±21 liters.
Ultrasound non-invasive sensor
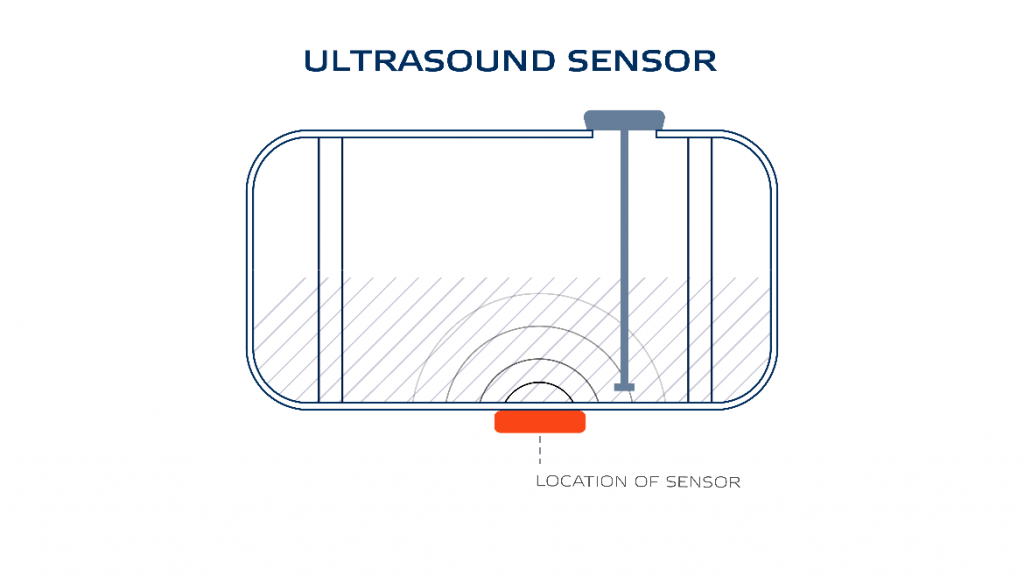
Measures the time it takes for an acoustic wave to travel from the bottom of the tank to the surface of the fuel and back. Attached externally underneath the fuel tank.
Advantages:
- Attached with acoustic glue; no need to drill or deform the fuel tank.
Disadvantages:
- Complicated installation; difficult to locate perfect spot to attach sensor.
- Glue takes 24 hours to set in a stable warm environment under constant pressure; glue may deform, weakening link between sensor and tank and leading to wave signal distortions.
- Can be dislodged by stones, water, sidewalk edges or deliberate interference.
- Signal gets lost on bumpy or steep roads; hard to aggregate trustworthy data.
- Sand and dirt on tank can make measurement impossible.
Capacitive sensors
The most popular fuel level control technology in the world. Originally introduced for the aviation industry, but now widely used across cargo and freight services, logistics, oil and gas, mining, construction and agriculture. These sensors measure the capacity of the coaxial-type probe condenser as it is filled with fuel.
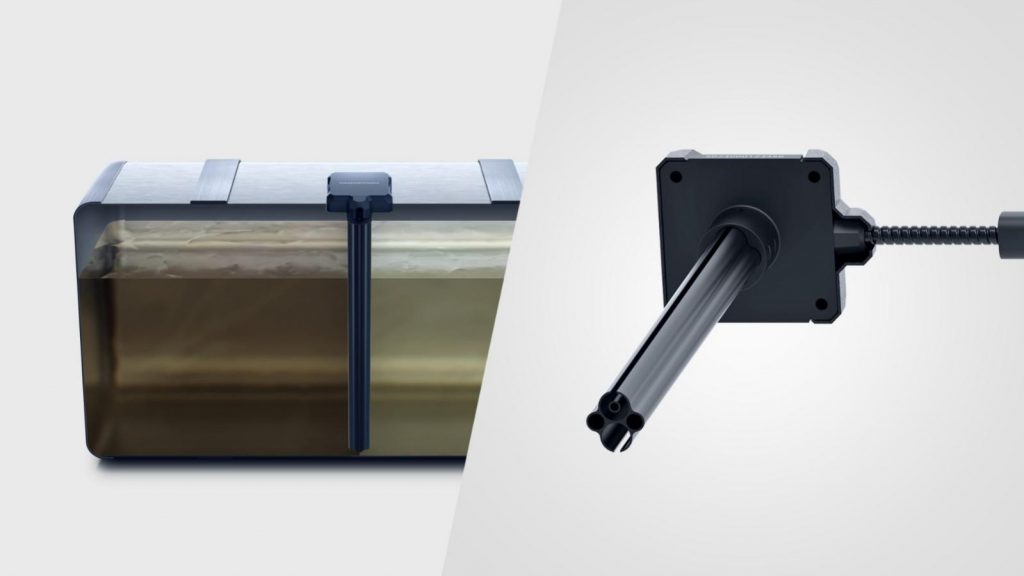
Advantages:
- Extremely reliable. No blind zones. Highly accurate.
- No mechanical parts to break; no need for maintenance over the sensor’s lifetime.
- Forwards real-time data on fuel levels, including information on refueling and draining events.
Disadvantages:
- Capacitive sensors are usually only accurate in relation to the fuel originally used for calibration. Switching fuel types requires recalibration.
- Installation in a fuel tank may void the tank warranty – but this does not affect the warranty on any other part of the vehicle.
However, the newest generation of capacitive sensors feature auto-adjusting technology to eliminate the recalibration issue due to fuel type or fuel chemical composition changes, and claim exceptional accuracy of 99.5%.
Choosing a fuel management solution is an important decision, and you should not invest in solutions that give you incomplete, inaccurate or unnecessary data.
Pick the solution that delivers top accuracy and that you can rely on in the widest possible range of conditions. Inefficient technology will not help you increase efficiency in your business and may even lead to further costs.
Do your research, and choose wisely!
Author
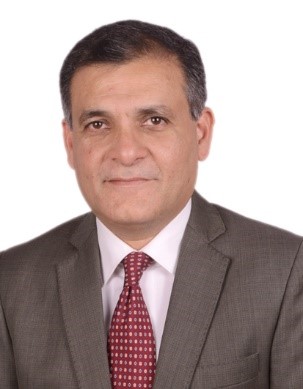
Mohit Mehrotra, Managing Director of OMNICOMM India- global leader in IoT fuel monitoring and analytics for commercial fleets, transportation, logistics, construction and more.
Published in Telematics Wire