Hardware meets software: from classic mechanical systems to a fully interlinked high-end control unit
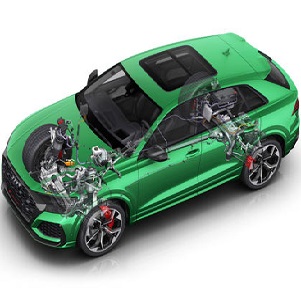
Exactly 40 years ago, Audi revolutionized the automotive world. With its permanent quattro all-wheel drive the company, in 1980, presented a new approach to chassis technology that still decisively underpins the slogan “Vorsprung durch Technik.” Today, thanks to smart interlinking by the Electronic Chassis Platform (ECP), innovative chassis systems such as electromechanical Active Roll Stabilization (eAWS), the predictive active suspension and Dynamic All-wheel Steering (DAS) are able to unfold their full potential. In the Audi e-tron, the integrated Brake Control System (iBRS) emphasizes the fact that efficiency will become the third variable in chassis development alongside ride comfort and sportiness. As a high-tech control unit, the future vehicle dynamics computer can simultaneously actuate up to 90 components.
On the road toward an integrated vehicle dynamics brain
Audi consistently drives the idea of integrating chassis and powertrain technology. In the future, an integrated vehicle dynamics processor will handle longitudinal and lateral dynamics control as well as energy and powertrain management: recuperating energy during a braking event, determining the damper compression rate within milliseconds and keeping the vehicle precisely on track – all practically at the same time. The development objective for future chassis generations is clear: besides an even greater spread between sportiness and comfort, the integration of efficiency technologies will play a central role.
The future vehicle dynamics processor will be centrally controlling nearly all functions in longitudinal, lateral and vertical dynamics: chassis, powertrain and recuperation functions, and be clearly more powerful than today’s ECP, for instance. It will operate about ten times as fast as current systems and be able to control up to 90 system participants – compared to about 20 in the case of the current ECP. New as well will be its modular usability for diverse types of powertrains, in other words, ICE-powered, hybrid or electric vehicles, as well as front, all-wheel or rear-wheel drive systems for electric models. As a result, the central vehicle dynamics computer, in addition to car-to-x functions, will enable function-on-demand features as well. Its precise data computation will also execute the requirements of advanced driver assistance functions.
Chassis technology development at Audi emphasizes intensified interlinking of individual mechatronic chassis components and vehicle functions using smart electronic control. The Electronic Chassis Platform (ECP) made its debut in the Audi Q7 in 2015. Today, it interlinks the individual component assemblies of the chassis systems in Audi’s mid-size, full-size and luxury models. Due to this smart ECP interlinking of chassis technologies that have undergone continuous further development such as permanent quattro all-wheel drive, the adaptive air suspension and Dynamic All-wheel Steering, Audi has forged a successful link between superior ride comfort and high-level driving dynamics.
Interlinking as an enabler – previously unknown flexibility, from comfortable to sporty
A perfect example that illustrates the enormous effort Audi invests in the technical design of the chassis is the electric roll stabilization used in the Audi SQ7 and SQ8. Due to smart interlinking, the system can unfold its full potential. Body roll of the full-size SUV during cornering and load changes is reduced to a minimum. In addition, it provides the Audi full-size SUVs with amazingly high lateral dynamics capabilities resulting in an impressive driving experience for the driver.
In fast cornering situations, due to the electronic adjustment of the stabilizer bar, body roll is reduced because the stabilizer, within milliseconds, smoothly lifts the vehicle side that is on the outside of a corner against the centrifugal forces with a moment of up to 1,200 Newton meters. This makes higher cornering speeds possible and clearly reduces load change reactions as well. During straight-line driving, for instance on uneven road surfaces, a planetary gear system disconnects the two halves of the stabilizer, which enhances ride comfort. As a central control unit, the Electronic Chassis Platform also matches information from other chassis technologies in the SQ7 and SQ8, such as the all-wheel steering system, the air suspension and the quattro sport differential. The driver experiences this close collaboration of the Audi chassis systems in the form of high handling precision and agility.
Another chassis highlight with a decidedly comfort-enhancing function is used in the Audi A8. Here the active suspension operates: a fully active, electromechanically operated suspension system. Per wheel, it has one electric motor that is supplied by the 48-volt primary electrical system. The control signals for the active suspension are sent by the Electronic Chassis Platform every five milliseconds. A belt drive and compact strain wave gearing convert the torque of the electric motor to 1,100 Nm and transfer it to a steel torque tube. From the end of the torsion bar, the force reaches the chassis via a lever and a coupling rod. At the front axle, it acts on the air spring strut of the adaptive air suspension and on the rear axle, on the transverse control arm (wishbone).
In this way, every wheel of the Audi A8 can be separately subjected to or relieved of additional loads and adapted to the respective roadway. As a result, it actively controls the position of the body in any driving situation. Due to the flexibility of the active suspension, driving characteristics are expanded to an all-new range. When the driver selects dynamic mode in the Audi drive select system, the car becomes sportier: it firmly turns into corners, the roll angles are only about half as big compared to the normal suspension, and the body hardly dips during braking events. In comfort mode, however, it smoothly floats across surface irregularities of any kind. In order to calm the bodywork, the active suspension constantly – adapted to the respective driving situation – supplies energy to or removes energy from the body. Thus, drivers and passengers are practically “disconnected” from mechanical powertrain and driving effects.
On the other hand, in the event of an impending side impact at more than 25 km/h, the active suspension of the A8 instantaneously lifts the body by up to 80 millimeters. As a result, the other car involved in a crash will only hit the sedan in an even more resistant area. The deformation of the passenger cell and impact on the occupants, especially in the chest and abdominal area, can thus be as much as 50 percent lower than in a side crash without suspension lifting. Here, again, the ECP is responsible for activating the active suspension and its interlinking with other chassis components like the air spring. The results: premium ride comfort and maximum safety.
Braking is a winner – the integrated Brake Control System in the Audi e-tron
The integrated Brake Control System (iBRS) of the Audi e-tron models illustrates the increasing intertwinement of chassis and powertrain technology. As a result, efficiency becomes the third objective of chassis development alongside comfort and sportiness.
The recuperation system, for instance, contributes up to 30 percent to the range of the electric SUV. The iBRS includes the two electric motors as well as the hydraulically integrated braking system in this process and is the first to combine three different types of recuperation: manual overrun recuperation using paddle shifters, automatic overrun recuperation using the predictive efficiency assistant and brake recuperation with a smooth transition between electric and hydraulic deceleration. The Audi e-tron recuperates up to 0.3 g exclusively via the electric motors without using the conventional brake – this is the case in more than 90 percent of all deceleration events. As a result, practically all normal braking maneuvers are energetically fed back into the battery.
Drivers can select the level of overrun recuperation in the Audi e-tron in three stages using the paddle shifters. On the lowest level, the car coasts without additional drag torque when the driver’s foot is lifted off the accelerator pedal. On the highest level, the electric SUV noticeably reduces speed – the driver can decelerate and accelerate strictly via the accelerator pedal, resulting in the so-called one-pedal feel. The brake pedal does not have to be used in this case of deceleration. The wheel brakes only come into play below the threshold of 10 km/h, when the brake pedal actuation exceeds 0.3 g or when the battery is fully charged and thus no brake recuperation is possible.
Due to a new electrohydraulic actuation concept, which Audi uses in an electrically propelled production automobile as the first manufacturer to do so worldwide, the driver can no longer perceive the transition from electrical brake recuperation via the electric traction motors to the mechanical braking effect via the hydraulically operated conventional friction brake. This “brake blending” results in an effectively variable pedal feel with a clearly defined, constant pressure point, just like in a vehicle with a conventional internal combustion engine and hydraulic wheel brakes. The brake pedal is not connected to the hydraulic system, the transition from the motor brake through the electric motors to the conventional brake is smooth and can no longer be felt by the driver’s foot.
This is enabled by a complex electrohydraulic system: a hydraulic piston in the compact brake module generates additional pressure and braking force that complements the recuperation torque. In an automated emergency braking event, only 150 milliseconds elapse between the time deceleration is initiated and the maximum brake pressure is applied between the linings and discs. Depending on the driving situation, the electrohydraulically integrated Brake Control System decides whether the Audi e-tron will decelerate by means of the electric motors, the wheel brake or a combination of both – electrically and individually on each axle. With this system the electric SUV makes specific use of its maximum recuperation potential.
Interlinking is emphasized in the integrated Brake Control System as well, with the iBRS being supported by the efficiency assistant that is provided as standard equipment. The system recognizes the traffic environment and route using radar sensors, camera images, navigation data and car-to-x information. As soon as it would make sense for the driver to lift his foot from the right pedal, respective information will be provided in the Audi virtual cockpit. In interaction with optional adaptive cruise assist, the efficiency assistant can also predictively decelerate and accelerate the electric SUV.
Glossary
adaptive air suspension
The adaptive air suspension – an air suspension system with controlled damping – offers a wide range between smooth ride and sporty handling. Based on speed and the driver’s preferences, it individually adapts to the road conditions and adjusts the ride height on different levels depending on driving mode and speed. The air suspension also offers level control as a function of load.
Active suspension
The predictive active suspension is a fully active, electromechanically operated suspension system with one electric motor per wheel supplied by the 48-volt primary electrical system. It can increase or reduce the load on each wheel individually to adjust to the road as needed. Consequently, the system actively controls the position of the body in every driving situation. The electronic chassis platform (ECP) sends control signals to the active suspension every five milliseconds. For predictive detection of the road conditions, it is connected to the front camera of the A8. The range of ride characteristics takes on a whole new dimension thanks to the flexibility of the active suspension: pitch movements of the A8 during acceleration and braking as well as body roll during cornering or load changes are minimized, which considerably reduces the effects of the drive train on the driver and passengers. In comfort+ mode, between 80 and 130 km/h, the body is inclined toward the inside of a corner by up to three degrees and thus reduces the lateral acceleration forces acting on the driver and passenger. When the driver selects dynamic mode in the Audi drive select mode, the system considerably reduces the body roll angles.
Audi drive select
The Audi drive select dynamic handling system allows drivers to experience different setups in their Audi. Choosing one of the modes – auto, comfort, dynamic or efficiency – changes the characteristics of important drive and suspension components from a comfort bias to distinctly dynamic or particularly fuel-efficient. In individual mode, drivers can configure the setup according to their personal preferences. Q and allroad models also include allroad and offroad modes, which, in combination with the adaptive air suspension, trims the car for driving off the beaten track.
Car-to-x communication
This is the generic term for diverse communication technologies – i.e. the exchange of information and data – in the areas of automotive and traffic engineering. Car-to-x stands for “car-to-everything,” in other words the transmission of vehicle information to third parties, i.e. other cars (“car-to-car” or “C2C”) or to traffic engineering infrastructure (“car-to-infrastructure” or “C2I”). Among other things, car-to-x communication serves the purpose of using the information and data transmitted by a vehicle to alert other road users to impairments (such as icy roads, traffic jams, etc.), but may also be used to create more detailed maps.
DAS (Dynamic All-wheel Steering)
An all-wheel steering system combines a rear-axle steering system with a regular front-axle steering system. At Audi, Dynamic All-wheel Steering marks an evolution of the system. It combines speed-dependent progressive steering featuring a variable steering ratio at the front axle with a rear-wheel steering system. The Electronic Chassis Platform (ECP) coordinates the front- and rear-axle steering systems. As a result, the steering angles on the front and rear axle can be adjusted independently. The rear axle, for instance, below 60 km/h, turns in the opposite direction by up to five degrees, which considerably increases agility in cornering and enhances handling in urban traffic: the turning circle of Audi’s premium-class models is reduced by 1.0 to 1.1 meters, depending on the type of car. Above 60 km/h, the DAS steers by up to two degrees in parallel to the front axle, which enhances straight-line stability. As a result, the DAS combines direct, sporty steering response with unshakeable stability, resolving an age-old conflict of aims exhibited by cars with rear-axle steering. Dynamic all-wheel steering is integrated into the Audi drive select dynamic handling system, where its characteristics, i.e. ratios and self-aligning forces, vary according to the driving mode selected.
DRC (Dynamic Ride Control)
Sport suspension plus with Dynamic Ride Control (DRC) is a particularly dynamic damping technology for selected Audi RS models. The single-tube dampers have a variable characteristic that the driver can adjust in three stages. The diagonally opposed pairs of shock absorbers are linked by hydraulic lines and a central valve. When cornering at speed, the valves regulate the oil flow in the shock absorber of the spring-deflected front wheel at the outside of a corner. They increase the support provided and reduce pitch and roll movements. This lets the vehicle hug the road more tightly and improves handling.
Dynamic steering
Dynamic steering varies the steering ratio based on the driving speed, steering angle and selected mode in the Audi drive select handling system. The central component is superimposition gearing in the steering column, which is driven by an electric motor. Known as strain wave gearing, its construction is compact, lightweight and torsionally rigid. It is free of play, precise and exhibits low friction. The gearing can transmit tremendous torques extremely rapidly and achieves a high level of efficiency. At low driving speeds – in city traffic and in maneuvering – the dynamic steering operates very directly; all it takes is two full turns to travel from end stop to end stop. The power steering boost is high as well, making parking maneuvers very easy. On country roads, the directness of the steering response and steering power assist are reduced progressively. At fast expressway speeds, indirect gear ratios and low power assist are used to smooth out unsteady steering movements to enable straight tracking.
eAWS (electromechanical Active Roll Stabilization)
Electromechanical Active Roll Stabilization (eAWS) ensures an extensive spread between smoothness of build-up and sporty handling. On the front and rear axle, between the two halves of the stabilizers, there is a compact electric motor with a three-stage planetary gear set. When driving straight ahead, the suspension control ensures that both halves of the stabilizer act largely independently of each other. This reduces the sprung mass vibrations on uneven roads, thus increasing ride comfort. At a sporty pace, however, the focus is on optimum roll compensation. The halves of the stabilizer act as a unit and are twisted in opposite directions by the transmission of the electric motor – the roll angle is significantly reduced when cornering, and the handling of the vehicle becomes even more firm and dynamic.
ECP (Electronic Chassis Platform)
The Electronic Chassis Platform (ECP) is the central control unit for the chassis. It records the speed, the height values, the vertical, roll and pitch movements of the car, the coefficient of friction of the roadway, the current driving state – such as under or oversteer –, and the data of the suspension systems involved. From these, it quickly calculates and precisely coordinates the optimal function of these components. Thanks to the central control, the customer experiences ride characteristics more distinctly in the form of precise cornering, improved dynamics and a high level of ride comfort.
iBRS (integrated Brake Control System)
The Audi e-tron is the first electric series-production model to use an electro-hydraulically integrated brake control system. The wheel brakes are actuated hydraulically, boosting is actuated electrically, and the activation is actuated electronically. The control unit detects with how much force the driver is depressing the brake pedal and, within milliseconds, calculates how much braking torque is needed. If the recuperation torque is not sufficient, hydraulic pressure for the conventional friction brake is generated in addition. A second piston produces the familiar pedal feel for the driver’s foot by means of a pressure-elastic element. Due to this brake pedal simulator, the driver is not affected by what is happening in the hydraulic system. In the case of ABS braking, pressure buildup and reduction are not noticeable in the form of parasitic hard pulsations in the pedal. The electro-hydraulic brake system is activated when the driver depresses the pedal on the left so hard that the deceleration exceeds 0.3 g; otherwise, the Audi e-tron decelerates through recuperation via the two electric motors. The brake control system builds up brake pressure for the wheel brakes with great precision and roughly twice as fast as a conventional system. When automated emergency braking is performed, there are only 150 milliseconds between the initiation of the brake application and the presence of maximum brake pressure between the pads and disks.
Permanent quattro all-wheel drive
The principle of four driven wheels is one of the supporting pillars of the Audi brand – and has been for 40 years. When the Audi quattro was unveiled at the Geneva Motor Show in 1980, it presented an all-new form of transmitting power in the passenger car sector – an all-wheel-drive system that was lightweight, compact, efficient and strain-free. As a result, the quattro principle was particularly suitable for sporty passenger cars and high-volume production – right from the beginning. Since the technology’s debut, Audi produced some 10.5 million cars with quattro drive by the end of 2019. Audi’s quattro technology is wide and varied and precisely tailored to the respective vehicle concept. quattro is an icon – the term stands for driving safety and sportiness, for technological expertise and for superiority in competition, in a nutshell: for Vorsprung durch Technik.
Sport differential
The sport differential provides for better driving dynamics, traction and stability. It actively distributes drive torque between the rear wheels, adding a self-locking center differential to the permanent quattro all-wheel drive. In addition to the features of a conventional differential, the sport differential integrates an internal gear and a multi-plate clutch with electrohydraulic actuation on the left and right. Depending on the situation, they force slightly different torque levels onto the rear wheels, resulting in a shift of the propulsion torque between left and right. In many Audi models, the sport differential is centrally controlled by the Electronic Chassis Platform. The software for the sport differential constantly computes the ideal distribution of torque at the rear axle for driving dynamics.