Explained: The Chip Shortage Problem And Its Impact On The Auto Industry
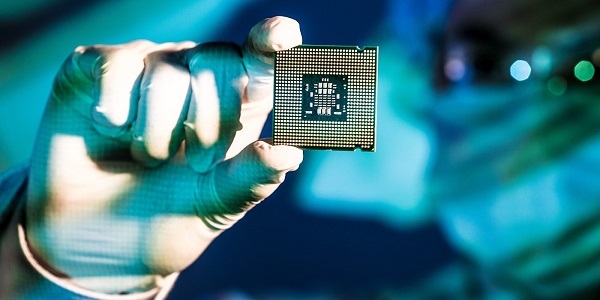
In the past two years, significant disruptions have occurred to the once sophisticated yet fragile automotive supply chain, starting with the COVID-19 pandemic and followed by a global shortage of semiconductor chips. Historically, the automotive industry regarded its robust supply chain as a crown jewel mastering the concepts of just-in-time, which meant thousands of components arrived just in time for assembly. This resulted in OEMs maintaining on-hand inventory of critical parts/supplies that lasted for just about 25-30 minutes of operations in the event that suppliers stopped delivering. Due to no practical inventory, the semiconductor chip shortage caused assembly lines to halt, causing a second major blow to the automotive industry after COVID-19. Based on our initial estimates, chip shortages could result in a loss of nearly eight million units of production in 2021.That said, it is critical to examine what has led to a shortage of semiconductor chips and what needs to be done to mitigate such events in future.
Understanding the Semiconductor Chips Ecosystem:
Semiconductor chips are highly complex products fabricated using advanced manufacturing processes. They are used to power and run a vast array of electronic devices – from smartphones, cloud servers, and consumer electronics to automotive vehicles, Industry 4.0 automation, and critical infrastructure and defense systems.
Needless to say, these little components are highly sophisticated and complex. Across the semiconductor industry’s value chain, our analysis indicates that companies invest 25-30% of their annual revenue in R&D, a ratio unmatched by any other industry, in addition to their extensive patent portfolios and large capital expenditures on equipment and operations. This clearly illustrates the depth and breadth of technical know-how necessary to lead and sustain in this high-tech industry. Because of the deep technical expertise required at every stage of production, the overall supply chain has become highly complex, intertwined, and geographically interdependent (as shown in Fig. 1). The US leads in the early stages of design and equipment manufacturing, while East Asian countries (South Korea, Taiwan, and China) lead in chip fabrication, packaging, testing, and assembly.
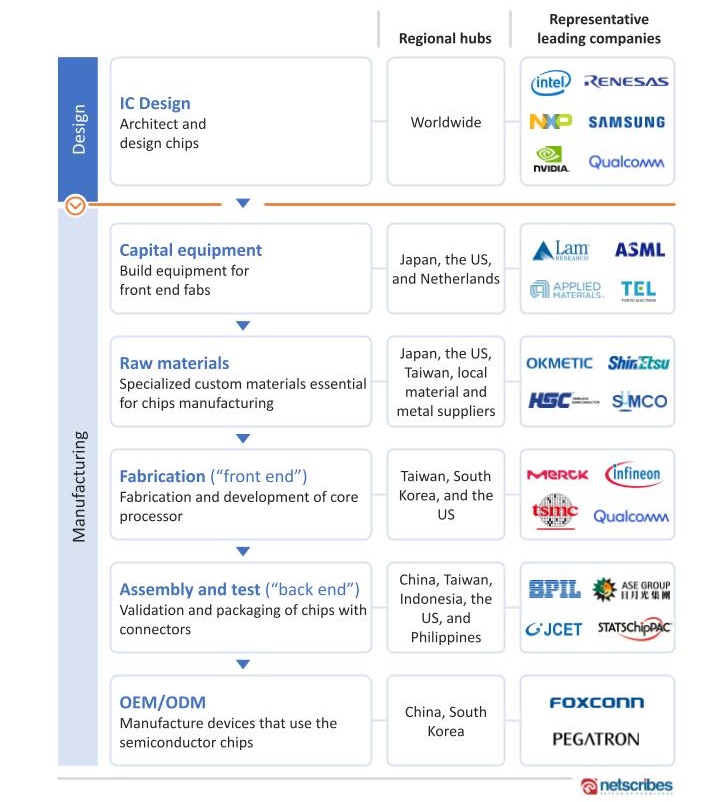
Fig.1: The semiconductor value chain is highly complex and fragmented
This global interconnected structure has led not only to optimum chip supply for various applications, but also to cost savings and performance enhancements at an exponential rate.
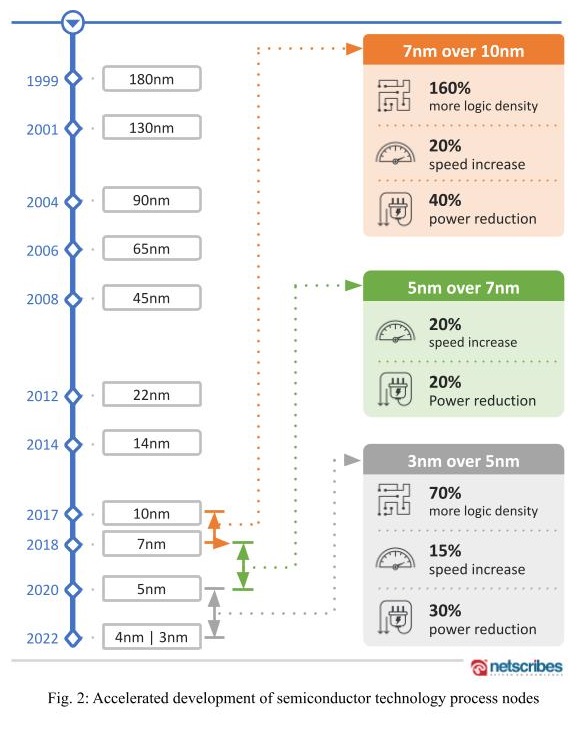
The complexity for the industry increases further as all the nodes still hold relevance for different industries and applications. For instance, trailing edge nodes (180nm – 40nm) are used by automotive and industrial OEMs for ADAS, autonomous, and other electronic features in vehicles and healthcare or production lines machinery built in 200 mm fabs. The advanced nodes (28nm, going down to 5nm and beyond) are used in wireless communications, servers, cloud computing and memory applications built in 300 mm fabs. According to industry association report, SEMI Fab Outlook, there are 10 new 200 mm fabs and 25 new 300 mm Si fabrication fabs expected to be operational by 2022, as what was in 2020. This is sufficient to indicate the foundries’ focus on generating high margins through leveraging advanced bleeding-edge technology nodes.
How did the semiconductor industry land in this situation?
A number of factors have combined to alter the predicted trends and dynamics of the industry. In recent years, there has been a constant demand for edge devices and secular factors, such as AI, cloud, IoT, Industry 4.0, robotics, and autonomous driving. These factors fueled the growth of semiconductor chips.
The COVID-19 pandemic has accelerated companies’ timeline for digital transformation, cutting short years of planned investment into a much shorter time frame. In addition, it provided the chip fabrication companies with a renewed growth vision from consumer electronics and work-from-home equipment, such as PCs, joysticks, gaming consoles, laptops, cloud storage, and webcams, to name a few.
Besides the usual business cycles, the industry has faced unprecedented turmoil from external factors, such as COVID-19 outbreaks, natural disasters, and changing consumer habits. Additionally, natural disasters like the Texas winter storm, Taiwan water crisis, fires in foundry facilities and the long-standing practice of automotive OEMs to engage in Just-In-Time (JIT) to keep costs low have contributed to the imbalance in the chips supply to OEMs across several industry and technology segments.
A ship blocked the Suez Canal for weeks, increasing logistics and freight costs by an average of USD 500,000 for shipping through South Africa’s Cape of Good Hope or shipping by air.
Consequently, the short-term industry dynamics are characterized by the following trends: insatiable demand for technology solutions and shortage of chips to meet the demand. Long-term perspectives go far beyond a few ‘transforming’ applications, but rather a structural shift in which global economies are becoming increasingly automated and digital. Connected smart edge devices, with the advent of cloud and AI computing approaches, are driving exponential growth in data volumes.
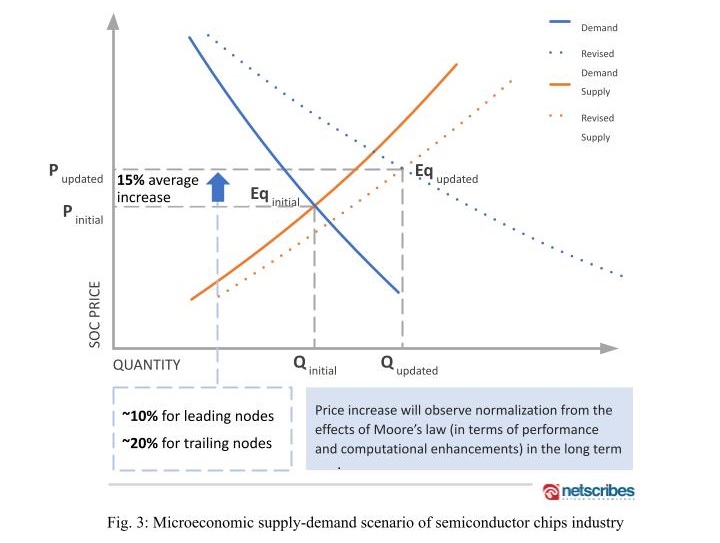
“There is a cascading effect about to set in. With huge influx of investments to increase the fab capacities and expansion plans, there is a long time to go before the returns start coming back in. This means, increase in prices of finished product at every node by around 15% and above, making the end customers shell out ~20-25% more from their pockets to purchase the same products with same features and specifications.”
- Saurabh Gupta,
Impact on the automotive industry
Although the automotive industry has always been cyclical in nature and directly correlated to economic volatility, most executives in this industry have learnt to prepare for and manage such shocks in the past. However, this time the backlash of COVID-19 and an unprecedented shortage of semiconductor chips has caught the industry off-guard. Fig. 4 showcases how the auto industry has evolved and its outlook.
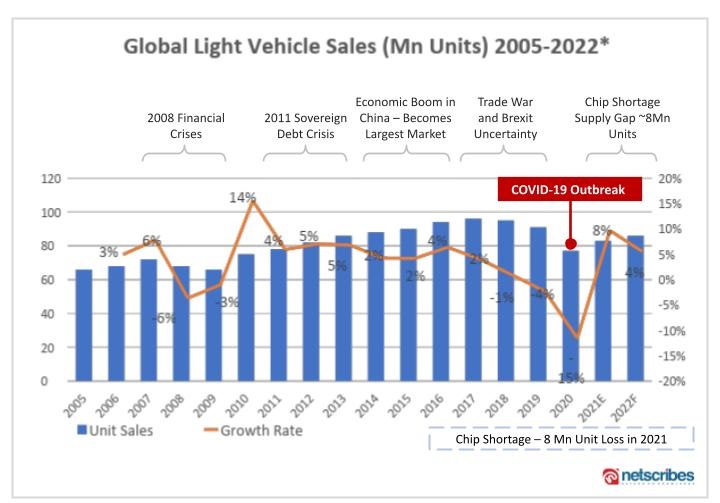
Due to a faster than expected rebound in demand for new cars, the auto industry was the first to experience the effects of a shortage of chips. This surge was contrary to industry OEMs’ forecasts, which had curtailed chips procurement at the start of the pandemic. Across the industry, it is known that a single chip wafer can take anywhere from three to six months to reach the OEM for assembly into the final product. This lead time and pre-allocation of chips has now become cumbersome for the industry. While companies like Ford, General Motors, Volkswagen, and BMW have stalled production, reduced vehicle production has also led to billions of losses across the industry. Ford estimates its operating losses will total USD 2.5 Bn for FY 2021, while General Motors anticipates losses of USD 1.5 to 2 Bn for the same period. The sales of a car were held up by a component worth no more than 1-2% of its cost.
“A nano-sized component worth not more than 1-2% of the car’s entire BoM cost has triggered the collapse of an entire multi-billion-dollar industry, and brought several production lines, assembly floors, and factories to the verge of shutdown.”
- Siddharth Jaiswal
The problem continues! With edge devices also increasing exponentially, consumer electronics and technology equipment also feel the strain of reduced chip availability. Companies like Dell and HP have witnessed its market share prices drop, while Apple announced losses worth USD 4 Bn because of lost sales in its Mac and iPad product line.
The way forward for the semiconductor industry
There’s also a flip to the overall story. Even though the demand has been at an all-time high, the semiconductor industry’s supply nodes have also been bottlenecks in the plan of meeting the demand. This has led to the foundries operating at near full utilization. Since Q2, 2020, foundries are consistently operating at over 90% utilization, which is not a sustainable long-term solution.
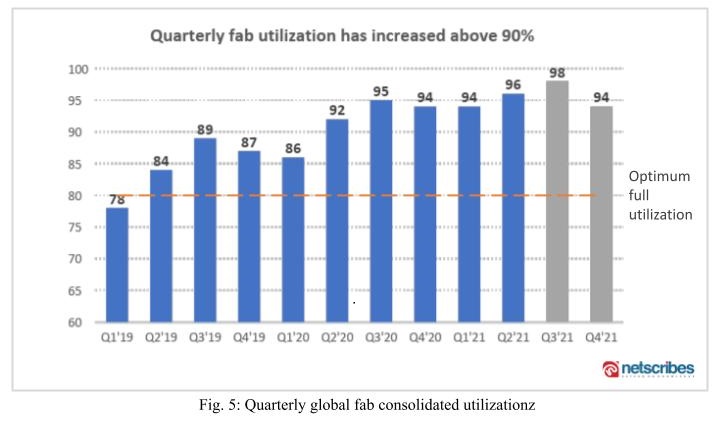
Thus, chip fabrication companies are left with a few alternatives, such as expanding existing fabs, building and operating new fabs, or distributing excess chip loading to alternative vendors. All of these, however, are not immediate solutions and will take anywhere from 12 to 36 months to materialize. While fab expansion costs around USD 4-5 Bn, building a new fab with R&D investment and equipment procurement costs nearly USD 30 Bn. In order to deliver long-term solutions, semiconductor companies and regional governments are in the process of finalizing investment budgets, policy incentives, and domestic buildup outlook. Leading foundries have budgeted almost USD 500 Bn to develop new chip fabrication fabs for different technology nodes globally, which is also influenced by the magnitude of incentives, tax regimes, talent pool available in various geographies. For instance, South Korea, already a leading region in the fabrication segment, has coordinated to invest USD 450 Bn over the next 10 years, apart from USD 1.3 Bn worth of tax breaks and funding of 36,000 new professionals.
Our analysis of the overall landscape indicates that the equilibrium between semiconductor chip supply and demand will reach anytime between 2023 and 2024. However, with neither the demand stabilizing nor the supply of chips increasing in the short term, there is a high probability of the similar shortage situation occurring again in the future. It is now up to the industry to come up with new innovative solutions to this sticky situation.
“The entire situation is still far from getting resolved. In fact, it will worsen further, with OEMs resorting to stockpiling and excessive ordering to increase their safety stocks, thereby piling up the demand orders for the chip production companies. Once this hoarding practice settles and actual demand is met, will the normal state come for the semiconductor industry. And that seems difficult before 2023 or 2024!”
- Saurabh Gupta
The way forward for the automotive industry:
With the situation showing no resolution in short term, the automotive industry would consider reducing the chip content per vehicle, i.e., ECU consolidation. Over the past few years, with the rise of electronic content and the transition to software-defined-cars, the existing patchwork approach is no longer sustainable. Hence, the industry is exploring new vehicle E/E architectures that enable not just high electronic content, but also support the road to autonomous vehicles (as shown in Fig. 6).
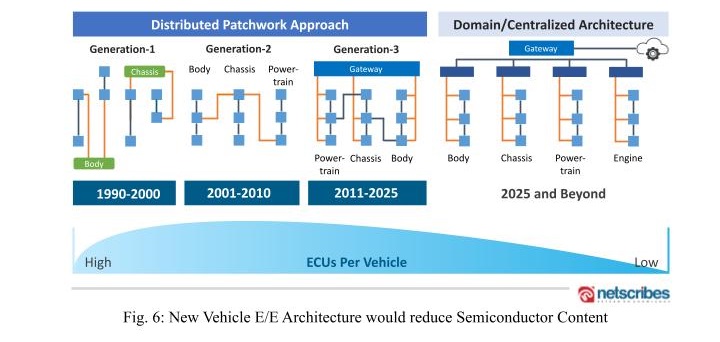
The average number of ECUs in a car range from 80-100 today, however, with the new vehicle E/E architecture, this number will drop to 20-30, thereby reducing the dependency on semiconductor chip(s) significantly.
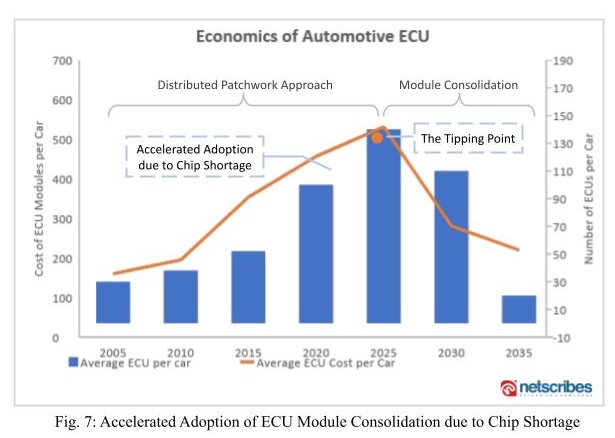
Additionally, to the above solutions, it’s time to streamline and reevaluate the strategies of companies across the entire value chain to ensure sustained growth and to avoid reentry into similar situations. The semiconductor industry should consider adopting a 5-R strategy: Rectify, Resiliency, Restore, Reimagination, and Refine. Maintaining business continuity plans, adjusting demand planning in real time, tracking competitive dynamics, updating product pricing, and assessing trade environments are all part of the job. Additionally, OEMs need to revisit their business and operations strategies to avoid being caught in such unforeseen circumstances again. Apart from enabling and implementing resiliency tools, such as collaborative planning and real-time market and industry monitoring for the identification of real-time bottlenecks, they should categorize the input raw material components, such as semiconductor chips, according to their impact and probability of disruption risk.
Author
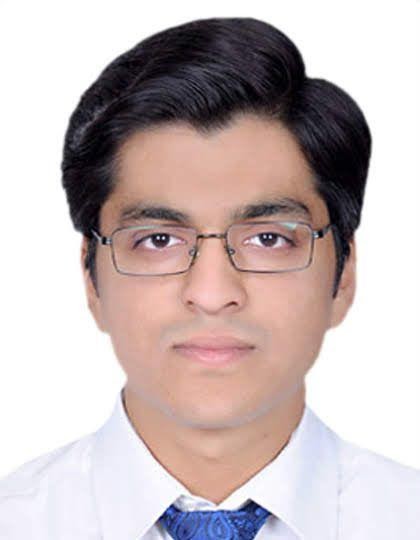
Saurabh Gupta
Research & Strategy Manager – Semiconductors
Netscribes
Saurabh has been in the strategy consulting and advisory role for more than nine years, working closely with semiconductor, electronics, and nanotechnology companies to solve their business and operational challenges. He is currently associated with Netscribes, working on providing actionable business and corporate strategies to the sales, marketing, IP legal, and operations teams of client organizations globally.
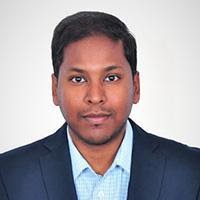
Siddharth Jaiswal
Practice Lead – Automotive
Netscribes
Siddharth has been tracking the automotive industry since the past nine years with keen interest in future of mobility, autonomous technology, and vehicle E/E architecture. He leads the automotive practice at Netscribes and works closely with the major automotive companies in solving some of the most complex business challenges.
Published in Telematics Wire