Engineering next generation Electric Vehicles through Virtualization
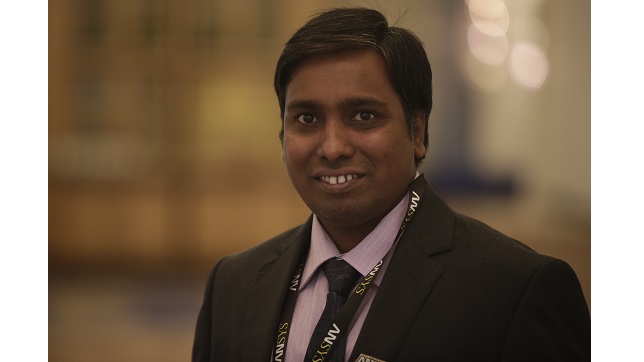
The last six months have been quite turbulent for the automotive industry globally, especially in India. These challenging times have given the industry an opportunity to evaluate and reprioritize the technological initiatives that could pave the way for the future. Electrification, which is one of the disruptive technologies for the automotive industry, is expected to see significant acceleration in localization. Some [REF] studies estimate the electric vehicle market to value around ₹500 billion by 2025. Two-wheeler and three-wheeler market may see significant adoption with more than 20%, followed by e-buses, which maybe around 13%. Light commercial vehicles may see a modest adoption in the medium term, but will ramp up as the infrastructure starts to settle in.
To meet the growing market demand, the engineering team in these organizations must combine speed with a strong commitment to deliver the product promise of reliability and performance. Engineering simulation has played a key role in enabling OEMs to realize these product promises. 3D simulation has established itself as a standard practice for detailed design of the components across the physical domains. CFD simulations have helped engineers to maintain the battery temperature within safe and reliable limits with optimized cooling system. Computational electromagnetics has been instrumental in ensuring the performance and validity of electric machines. Virtual pre-compliance testing for EMI EMC reduces the number of prototypes required to certify the product. Multiphysics simulations have helped engineers to understand the complex interactions of the different physical domain.
3D simulation, even though very powerful, cannot extend beyond component design as it cannot account for interactions with the control software and hence system performance parameters such as drive cycle analysis, range prediction etc. require a broader approach that extends beyond just 3D simulations. Automotive companies are working towards closing this gap by employing next generation simulation technologies.
I will now share some of my personal experiences while interacting with these OEMs/Suppliers and the trends that are emerging in product development process using virtual product development and validation techniques.
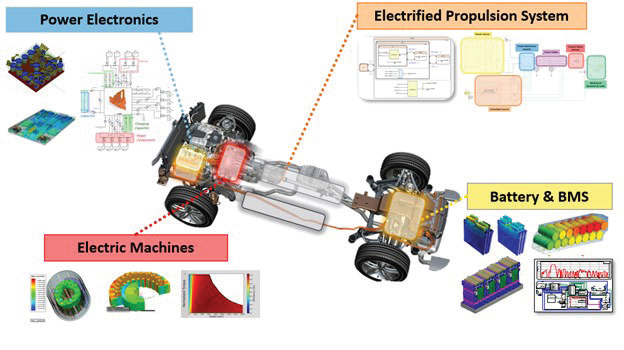
Model Based Design
The challenges in development of next generation vehicles lies in the increased complexity of the overall system. The complex functional and architectural designs need to be verified and validated for suitability early in the design cycle before venturing into complex and time-consuming geometrical design. Virtualization needs to extend upstream of the product development cycle to bring the system considerations early on in the design stage.
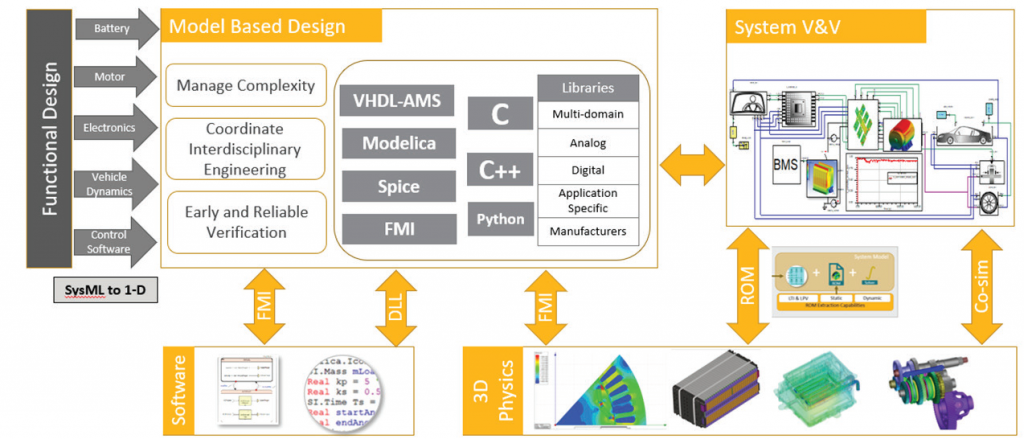
Model based design is the best way to tackle these challenges. It is known to reduce the complexity of the design while ensuring interdisciplinary interactions. The capability to perform early stage validation and verification ensures that none of the architectural issues are taken into the detailed design stage. This ensures that the detailed component design happens with much reliable design specification resulting into less design iterations. Opensource Modelling languages such as Modelica and VHDL-AMS are being used to develop EV component representations. Model exchange standards of Function Mock-up Interface (FMI) helps collaboration across the simulation platforms. Even historical design and test data can be used through data analytics and machine learning to create accurate behavioral model
Physics Based Virtual System V&V
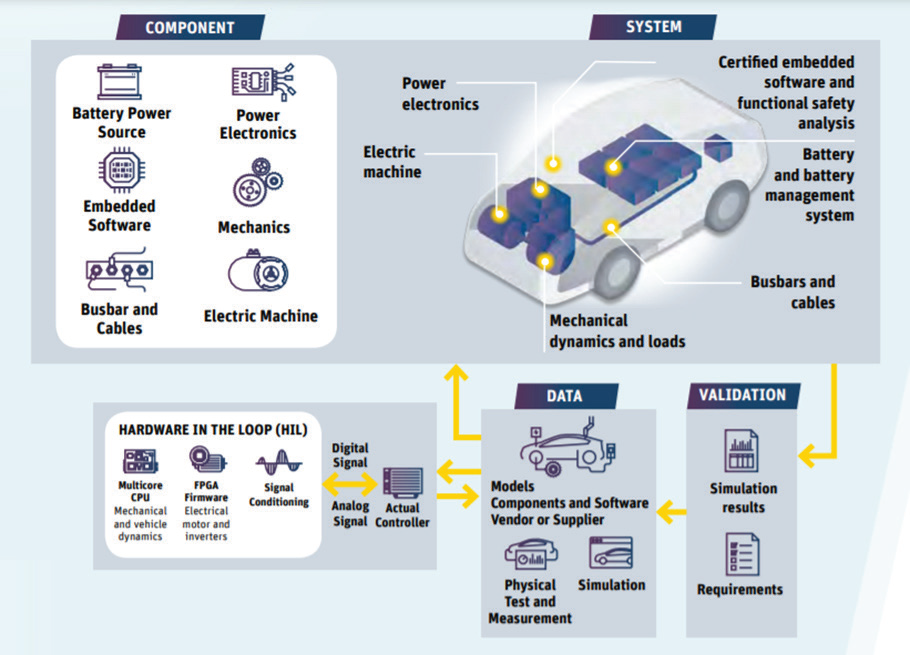
It is often encountered that a component designed in isolation exhibits the best in class performance, but when integrated into a system, shows significantly sub-par attributes. The complex interactions and interdependence between the components require component validation and design optimization on a system level. System validation and verification is an important milestone in product sign-off.
The traditional way of detailed system validation study is done after making physical prototypes of components and this makes any design change very expensive. Virtual validation and verifications, which can be done at an early stage, requires accurate representation of the components to ensure the accuracy in predictability of the system. Model Based Design can form the base of System simulation. As the product design matures, more and more high-fidelity data generated which can be used to improve the system model. The advanced techniques such as Reduced order Modelling (ROM) have proven to develop very accurate model representations from geometric simulation data. For complex simulation, such as prediction of battery temperature over a drive cycle or estimating motor performance for a given driving scenario, the ROMs have proven to accelerate the simulation speed without compromising the accuracy.
There is as much software in current vehicles as the hardware. Model based software development is widely used to develop the control software. The Battery management System (BMS) is the most critical piece of software in electric drivetrain. The functionality and the safety of the battery is determined by how well BMS performs its functions. Another important software code is motor controller, which is responsible for efficient operation of the electric machine. Apart from these, there are several vehicle level ECUs that manage the overall operation of the vehicle. These software algorithms, once implemented, needs to be verified with the plant model through Model-in-loop (MiL), Software-in-loop (SiL) or Hardware-in-loop (HiL) interfaces. The accuracy of the plant model developed for these validations is very important to ensure the software integrity.
Process Integration and Design optimization (PIDO)
Robust Design optimization (RDO) needs to pan across the complete product design workflow to ensure the optimal system performance across different physical and design parameters. RDO ensures the balance between product reliability, performance, and cost. PIDO can help to create infrastructure required for RDO. The ability of PIDO to integrate heterogeneous simulation environments from different sources to create a streamlined simulation workflow can prove very powerful when combined with RDO. PIDO yields substantial productivity gains for expert analysts and captures their expertise and makes it available to engineers outside the analysis department.
Model Based System Engineering: Platform for Digital Continuity
The advanced simulation techniques discussed before need a platform to enable seamless exchange of data and connectivity with the overall product development ecosystem. Model Based System Engineering (MBSE) provides the platform to achieve digital continuity between these different segments of product development and enables collaboration between them. The MBSE environment can interface with Application Lifecycle management (ALM) for connectivity with requirements and functional design. It can interact with Product Lifecycle Management (PLM) for geometric connectivity. Virtual as well as physical test data can be hosted on a Simulation Data Management environment (SPDM), which is at the heart of MBSE. This kind of framework will enable connectivity, traceability and interoperability throughout the product development lifecycle and enable a better and cohesive effort in product realization.
Author:
Tushar Sambharam has over sixteen years of experience in modelling and simulation domain of traction motor, wireless charging, power electronics. Tushar has worked extensively in enabling major Indian automotive OEMs and suppliers with adoption of advanced simulation methods. Tushar has developed several innovative modelling techniques using multiphysics, optimization and system simulation to solve EV challenges. He has several conference publications to his credit.
Published in Telematics Wire