Electric Vehicle Battery Management System and Chargers
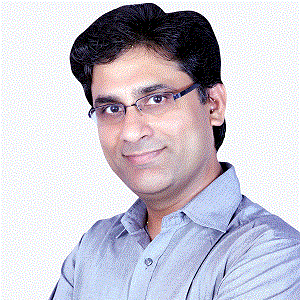
Introduction
The electronics content has been steadily increasing over the last two decades in the automotive segment. The existing market of Integrated Circuit (IC) is not just limited to advanced driver-assistance systems (ADAS), Infotainment & telematics, Chassis & Safety, Powertrain or Convenience, but also the hybrid and fully electric vehicles (EV) market are gaining momentum. The present worldwide automotive semiconductor market is about $38B in 2019, and the market may grow to $75B in the next 10 years considering 7% CAGR.
Today the size of the EV market is less than 3% of the total light vehicle market. According to one study, there may be about 120M EV by 2030 in the USA, Europe, and China. The average semiconductor content in the EV may increase by about 90% from the internal combustion engine (ICE) cars. The automotive electric vehicle infrastructure market could be about $25B in the next five years. The important building blocks of EV are chargers and Battery management system (BMS).
EV Chargers
The challenge that the EV faces is the battery charging time and battery life. Comparatively, the petroleum-based vehicles take less time to refuel the vehicle as compared to the EV. The level 1 charger has a charging capacity of less than 5KW, the fast-chargers have charging capacity between 5-50KW, and the super-chargers have a capacity of greater than 50KW. The higher capacity chargers take less time to charge the EV battery but it gets very costly and takes much area. The large battery capacity gives more driving range, but it comes with the increase in EV cost.
There are some issues related to faster charging. The fast charging may heat the series resistance of the battery and that may lead to fire hazard. Also, the fast charging may reduce the life of the battery if the battery temperature is not controlled in the desired range.
There are broadly two types of chargers designs available in the market: AC charger and DC chargers. There is a lot of research that is happening on the inductive charging. The AC chargers or the onboard chargers take the input AC supply and convert it into DC supply voltage to charge the battery. While the DC fast chargers deliver DC power directly to charge the battery. The level-3 fast charger may use a three-phase AC supply to convert into DC voltage. Both AC, as well as DC chargers, use a DC-DC converter to convert it into a suitable voltage to charge the battery safely. The theory behind AC/DC charger is similar to the primary flyback converter where the current in the primary is controlled to set the output DC voltage with desireddesire load (battery) current. Both the output feedback voltage and the load current is used in the control loop to stabilize the output voltage. Presently, many IC design houses design use sophisticated digital control to process feedback signals to control the power device.
To reduce the charging time, there can be an intermediate storage entity to store the DC charge instantly before the charge can be transferred to the battery through the charger. This transfer of charge from the intermediate storage space to the battery can be done at a slower speed. It can solve the issue of charging time and battery life.
Battery Management System
The Battery Management System fundamentally takes care of two parameters: 1) accurately sensing voltage and currents of the cells. 2) Battery thermal management system. The first part senses the voltage and current of each cell of the battery pack and then systematically transfers the information to the processor. The processor then compares it with the reference voltage and controls the gate of the power device during the charging operation. The processor also takes care of the safety operations of the battery like over-voltage, over current, short circuit current, over-temperature, and many more protections. It is critical to keep the temperature of the battery in the specified range else it may destroy the battery cells and significantly reduces the battery life.
The digital part of the ASIC may be designed in lower geometry. According to one of the reports, NXP and TSMC are collaborating on their next-generation automotive processor design in the 5nm TSMC process. The high voltage switching is usually done using discrete devices. Super Junction MOSFET can be used for switching up to 1kv and lower power. IGBT can be used up to 3kv and few megawatts of power. Thyristors can handle more power than IGBT.
Reference:
- AdvancedElectricVehicleFast-ChargingTechnologies, (May 2019, Energies, MDPI) Ryan Collin, Yu Miao , Alex Yokochi , Prasad Enjeti and Annette von Jouanne
- Charging ahead: electric- vehicle infrastructure demand, Oct 2018, McKinsey & Company
- NXP Selects TSMC 5nm Process for Next Generation High Performance Automotive Platform, June 2020
Published in Telematics Wire