Continental’s hose and line business on track for low-emission and zero-emission mobility
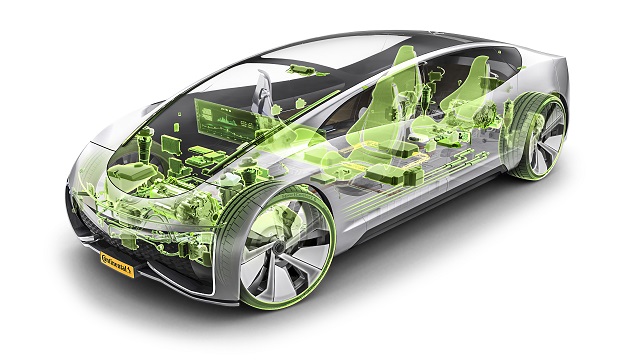
The technology company Continental has announced a new strategy for its hose and line business revolving around two primary objectives: “On the one hand, we are more strongly targeting eMobility as a major growth market. On the other hand, we are committed to helping automotive manufacturers further reduce emissions and meet increasingly strict emission standards,” explains Philip Nelles, Head of Mobile Fluid Systems – the business unit at Continental responsible for automotive hoses and lines. “Hoses and lines are absolutely essential factors in achieving emission-free and low-emission mobility. This is where we are stepping in to make an important contribution to sustainable mobility, and our order books are already reflecting this. Last year, alone, we received orders worth roughly 275 million euros for hoses and lines to be used in battery and hybrid drives for vehicles produced by German, Asian and North American manufacturers,” he continues. The reason for this trend is rising global demand for zero-emission electric and hybrid vehicles.
Sophisticated thermal management extends ranges of electric and hybrid vehicles
A major feature of Continental’s lines and hoses is sophisticated thermal management. This is driven by the fact that batteries in electric vehicles are most efficient when operated at temperatures ranging from 20 to 40°C. Battery life can be increased by either cooling or heating batteries in response to ambient temperatures. This leads to complex circuits which place significantly greater demands on individual components, including hoses and lines. Hoses and lines help to keep batteries and highly sensitive control circuits cool in electric and hybrid vehicles. Among other things, this has a beneficial impact on the range of battery-powered vehicles.
“We also achieve important weight savings thanks to an optimal mix of materials. After all, the less a vehicle weighs, the less energy is lost during acceleration and braking, and the further it can travel,” explains Nelles. Lines of smaller cross-section – for example on the high-pressure side and in battery cooling lines – save weight due to less coolant being needed than with earlier systems. The right mix of rubber, polyamide and aluminum materials and efficient line geometry ensure adequate inherent stability of the resulting systems. Towards this end, high-performance plastics are used in the engineering of Continental’s lines and connecting elements.
Continental’s future-ready hoses and lines also benefit from the company’s worldwide efforts to enhance its plastics expertise. “We aim to be in pole position when it comes to meeting the needs of the promising eMobility growth market. This is why we need state-of-the-art development centers and engineers dedicated to trailblazing the future, and that is precisely what we have,” asserts Nelles.
Another promising application for Continental’s high-tech lines is for air conditioning systems utilizing R744 as the most climate-friendly refrigerant available today. These next-generation lines help to save weight while regulating the temperature of the passenger compartment in a highly efficient and climate-friendly way. As an integral part of a vehicle’s temperature management system, they contribute to increased efficiency and range.
Low-emission mobility: Hoses and lines to facilitate compliance with increasingly stringent emission standards
Continental also helps automotive manufacturers in the quest to meet increasingly stringent exhaust and emission standards. “Our efficient hose and line systems are helping customers to consistently and sustainably lower emissions of hydrocarbons, carbon and nitrogen oxides and particulates, for example by means of exhaust purification technologies involving particulate filters or selective catalytic reduction (SCR),” explains Nelles. Lower weight also translates into lower emissions.
Continental’s engineers are achieving further weight reductions while at the same time improving performance. Plastic components reduce vehicle weight, thus contributing to lower fuel consumption and reduced carbon emissions. Similarly, plug-in hybrid drives currently in high demand are shrinking the amount of under-the-hood space needed for combustion engines and their ancillary components. This, in turn, is leading to elevated requirements for the lines and connectors involved, due to increased pressure and thermal loading in lighter, highly supercharged (downsized) drives.
For example, ancillary components used in newly developed internal combustion engines have to withstand temperatures of 160°C over 3,000 hours of continuous use, as well as peaks of up to 210°C. High-performance plastics such as heat-stabilized polyamide fully meet these requirements. In many cases, very thin-walled, formable stainless-steel tubes represent the best compromise between durability and weight reduction for turbocharger applications.
Growing demand for clean, emission-free mobility
As an example of just how dynamically the market is growing, Germany’s Federal Motor Transport Authority reports 194,163 new registrations of electric cars and 200,469 of plug-in hybrids in 2020. Compared with the previous year, this amounts to twice as many new registrations of electric cars, and more than triple the figure for hybrid models. The latest Continental Mobility Study also documents rising demand. According to the study, customer interest in buying an electric car in Germany has more than doubled since 2013, leaping from 17 to 35 percent. Another finding of the study: Market receptiveness to electric vehicles is even far greater in the Middle Kingdom, with 86 percent of all respondents in China indicating they could imagine buying an electric car. “This could also give electromobility a major boost,” comments Nelles in summing up the outlook for market growth in Asia.
“In order to be able to optimally serve this fast-growing market, we have strategically realigned ourselves internally, bundled our know-how and at the same time strengthened our cooperation with external partners,” adds Nelles. The JoinPlas joint venture launched last year with aft automotive, for example, focuses on the manufacture of couplings of new design using plastics specifically adapted to the application. Production of these is scheduled to start in Germany as early as the end of 2021.
With the Carbon Neutral for Emission-free Vehicles program announced at the beginning of December 2020, Continental is the world’s first automotive supplier to combine the two topics of emission-free mobility and carbon neutrality – and thus set a new, ambitious industry benchmark. As part of Carbon Neutral for Emission-free Vehicles, all of Continental’s business generated with products for emission-free cars, buses and trams – in other words, zero-tailpipe-emission vehicles (ZTEVs) – will be produced on a carbon-neutral basis from the beginning of 2022.