Automotive Semiconductor Demand Dynamics and Outlook
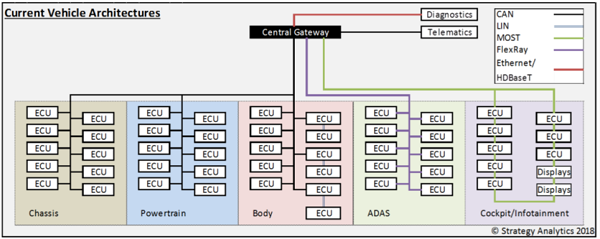
Exhibit 1 Typical Distributed E/E Architecture
The modern vehicle architecture has evolved over the years with the amount of electronics increasing across the powertrain, body, chassis, safety, and driver information domains. Present vehicle architecture topologies typically consist of various ECUs which are then connected to actuators, sensors and displays. These distributed, decentralized E/E (electrical and electronic) vehicle architectures have typically incorporated one electronic control unit (ECU) per function / feature, with a new ECU is added each time a new function / feature is added.
With low end vehicles having 50+ ECUs, mid-sized vehicles 80+ ECUs and high segment vehicles with 110+ ECUs, the automotive semiconductor content has increased over the years with demand for semiconductors extending across all device types and includes processors, power, linear, optoelectronics, memory etc. Meanwhile, the move towards electrification is serving as a catalyst towards increasing semiconductor content per vehicle with increasing demand in particular for power electronics. Electrification is underpinning new platforms that include typically also include implementation of advanced infotainment, ADAS (Advanced Driver Assist Systems) and autonomy.
Strategy Analytics has been covering the complex global automotive electronics market for decades, providing deep coverage at the system, semiconductor, and sensor levels, as well as a broad view of whole value chain. Strategy Analytics’ analysis concluded that global demand for automotive semiconductors in 2020 based on OEM vehicle production dropped by 9.7% to $37.9B, averaged across all applications and including sensors. The steep decline was reflective of the impact of COVID-19 pandemic felt by the industry, with complete production shutdowns occurring in the major light passenger vehicle production centers in the second quarter of 2020. Despite this production fall the continued growth in electronics penetration and sensing and control sophistication, especially in electrified powertrains, and to a lesser extent, ADAS/autonomous technologies continued. Indeed, semiconductor company financial reporting all pointed to significant improvements in their automotive revenues for the second half of 2020 and this continued into 2021 as shown by Strategy Analytics quarterly automotive revenue index.
Strategy Analytics’ Revenue Index, Profitability Index and Automotive Semiconductor (Auto Semi) Index look at the quarterly financials as posted by ten of the leading publicly quoted automotive semiconductor companies. Collectively, these ten companies accounted for 64.5% of the global automotive semiconductor market in 2020 as presented in Strategy Analytics’ annual Automotive Semiconductor Vendor Market Shares analysis.
Exhibit 1 Strategy Analytics Automotive Semiconductor (Auto Semi) Index
Strategy Analytics
The Strategy Analytics Auto Semi Index looks specifically at the automotive revenues for these companies. Using Q1 2019 results as a baseline set to 0, subsequent quarterly results for each of the companies are measured against this baseline with results above 0 indicating growth and results below 0 showing a contraction in revenues.
In 2021, automotive semiconductor demand was forecast to see a steep return to growth with the market forecast to grow as demand for vehicles returned across all regions, augmented further by continued momentum towards electrification. This forecast outlook included an anticipation of vehicle production stabilising globally, but ongoing risks associated with the shortage in semiconductor supply as well as additional waves of the COVID-19 pandemic hitting regional production centres are serving to temper the recovery.
The demand for semiconductors from the automotive industry extends across all device types and includes processors, power, linear, optoelectronics, memory etc. While individual occurrences such as industrial action or accidents can have an impact on the supply of semiconductors and chipsets for specific applications, these do not constituent the primary cause of the current shortages being experienced by the automotive industry. Instead, the primary cause can be traced back to vehicle production shutting down in the second quarter of 2020 resulting in automotive semiconductor demand being scaled back considerably as reflected in the sharp contraction observed in the Auto Semi Index.
A return in demand was led by Chinese vehicle production and was followed by a return to production in the other major production centers resulting in a sharp expansion in automotive semiconductor demand. However, the automotive industry was then faced with several issues in trying to make up both a shortfall as well meet the resurgent demand having effectively taking itself out of the queue for semiconductor supply.
- Changes in working and lifestyle patterns due to lockdowns shifted the focus for semiconductor suppliers towards supporting electronics equipment demand for smartphones, IT and audio-visual equipment as well as the introduction of new generation consoles from Sony and Microsoft.
- The dedicated semiconductor manufacturing capacity available for the supply of 8-bit, 16-bit and 32-bit MCUs, based on older process nodes and smaller diameter production, was quickly filled up and this was then further compounded by further constraints in the material supply chain.
- With volume demand from the automotive industry paling in comparison to the demand from mainstream electronics, the major semiconductor suppliers naturally prioritized demand from the smartphone, IT, audio-visual and other consumer electronics, making it difficult for the automotive industry to move from the back of the queue.
In the first quarter of 2021, there were a further confluence of events that conspired to further impact semiconductor production including an earthquake in Japan and snowstorms in Texas, US. Another factor that semiconductor manufacturers needed to account for was a drought in Taiwan.
A fire at a Renesas facility represented another setback for the automotive supply chain (with companies such as Ford specifically referencing Renesas during their discussions of the semiconductor supply situation in management comments). Production at the affected 300 mm Renesas line is focused on MCUs and SoCs targeting automotive, industrial and other applications. An early assessment from Renesas suggested that the resumption of normal production would take at least one month but this was later revised to three months.
- Renesas moved some production to other facilities as well as seeking additional support from its foundry partners allowing limited production to resume in April.
There was also an accidental power cut at one of TSMC’s facilities though the company’s initial observations were that production was not impacted too much.
As we moved into the second half of the year, most of the semiconductor suppliers were able to report improving conditions as far as front-end semiconductor production was concerned.
Companies such as Infineon that had to shut down facilities in the first quarter of the year because of the snowstorms in the US reported that they were operating at pre-shutdown levels with revenues not fully able to capture the underlying growth opportunities. Renesas had ongoing issues with returning production at the N3 Building (300mm line) of its Naka Factory (located in Hitachinaka, Ibaraki Prefecture) to the output levels prior to the fire. In particular, the company has suffered a series of problems since then with manufacturing equipment which resulted in shipments levels (as reported on July 29) falling to 90% of the volumes prior to the fire.
Despite these challenges, Infineon, Renesas and the other semiconductor suppliers were able to report increases in revenue, gross margin and operating margin for its automotive business as well as a growing order backlog. Unfortunately, the bottleneck at the frontend was replaced with headwinds at backend processing facilities as a resurgence in COVID-19 cases at backend manufacturing and R&D operations in Malaysia, India and Taiwan hampered the ability of the automotive semiconductor industry to meet both current and ongoing demand over the forthcoming quarters.
The combined impact of semiconductor shortages in general, combined with these other events served to limit the much-vaunted recovery in light vehicle production. Major OEMs have steadily increased the frequency at which they are reporting adjustments to their production schedules citing the ongoing impact of semiconductor shortages. Even those companies that were initially better prepared, e.g., Toyota are now regularly advising of adjustments to their production lines as the impact of the semiconductor shortage has snowballed. This has also resulted in OEMs adopting a range of measures to alleviate the situation which include:
- Temporary shutdown of production lines.
- Ongoing reduction in shift hours through the next six to nine months.
- Allocation of semiconductor and other resources to production lines focused on the most profitable and/or high-volume brands and nameplates.
- Vehicles produced but with final finishing delayed until certain components are secured.
- Vehicles produced with certain non-critical components missing that allow a vehicle to be finished with the final production vehicle noting a minor reduction in aesthetics, performance or fuel economy.
Strategy Analytics analysis of the ongoing challenges in the supply chain suggested that this would result in vehicle production being impacted further than originally estimated with the loss in production attributable to semiconductor constraints as high as 5 – 10% for 2021. Comments from TSMC, automotive OEMs and the broader supply chain earlier in the year suggested that while the overall semiconductor shortage may last into 2022 and possibly even through to 2023, the situation for the automotive industry would start to see signs of improvement from Q3 onwards limiting the overall impact to light vehicle production.
Unfortunately, as we start to see calendar year third quarter financials being released at the time of writing, it does appear that the combined impact of semiconductor shortages, a resurgence in COVID-19 and other associated issues around materials supply will translate to actual vehicle production growth being curtailed to around 3% to 5% year-on-year. At the same time, automotive semiconductor suppliers look set to continue reporting robust financials for the third quarter suggesting that there is a growing mismatch between automotive semiconductor industry revenues and actual vehicles being produced. Regrettably, this raises the possibility that despite the best efforts of the supply chain, double bookings will lead to excess inventory in play that will serve to limit automotive semiconductor industry growth in 2022 and 2023.
Longer term, the prospects for automotive semiconductor demand remain strong, led as stated earlier, towards trends that favour vehicle electrification, ADAS (Advanced Driver Assist Systems) and Autonomy and connectivity. This means that the average semiconductor content in a vehicle will grow at a CAAGR (compound annual average growth rate) of 6.2% over the 2020 – 2025 timeframe. The move towards electrified platforms in particular dictates an increasing weight given towards power semiconductors. The incumbent power semiconductors are Silicon-based IGBTs (insulated gate bipolar transistor) and MOSFETs (metal oxide semiconductor field effect transistor) and leading suppliers of these power semiconductors include Infineon, Rohm, STMicroelectronics, ON Semiconductor and others. These incumbent technologies are starting to see growing competition from wide bandgap technologies such as SiC (silicon carbide) and GaN (gallium nitride) and this trend is accelerating over the next five to ten years with all the major suppliers of power semiconductors investing in these wide bandgap technologies as they see increased demand. By 2028 electrification and ADAS will account for 50% of automotive semiconductor demand and this will translate to the growing demand for power semiconductors and advanced processor chips.
Exhibit 3 Automotive Semiconductor Market 2019 and 2020
Strategy Analytics
Despite the short-term challenges being faced presently, rising vehicle production and associated system demand will translate to the forecasted compound average annual growth rate (CAAGR) for automotive semiconductors, including sensors, over the 5-year period 2020 to 2025 to be +12.4% with the market holding potential to be worth between $77 to $81 billion by 2028.
About the Author
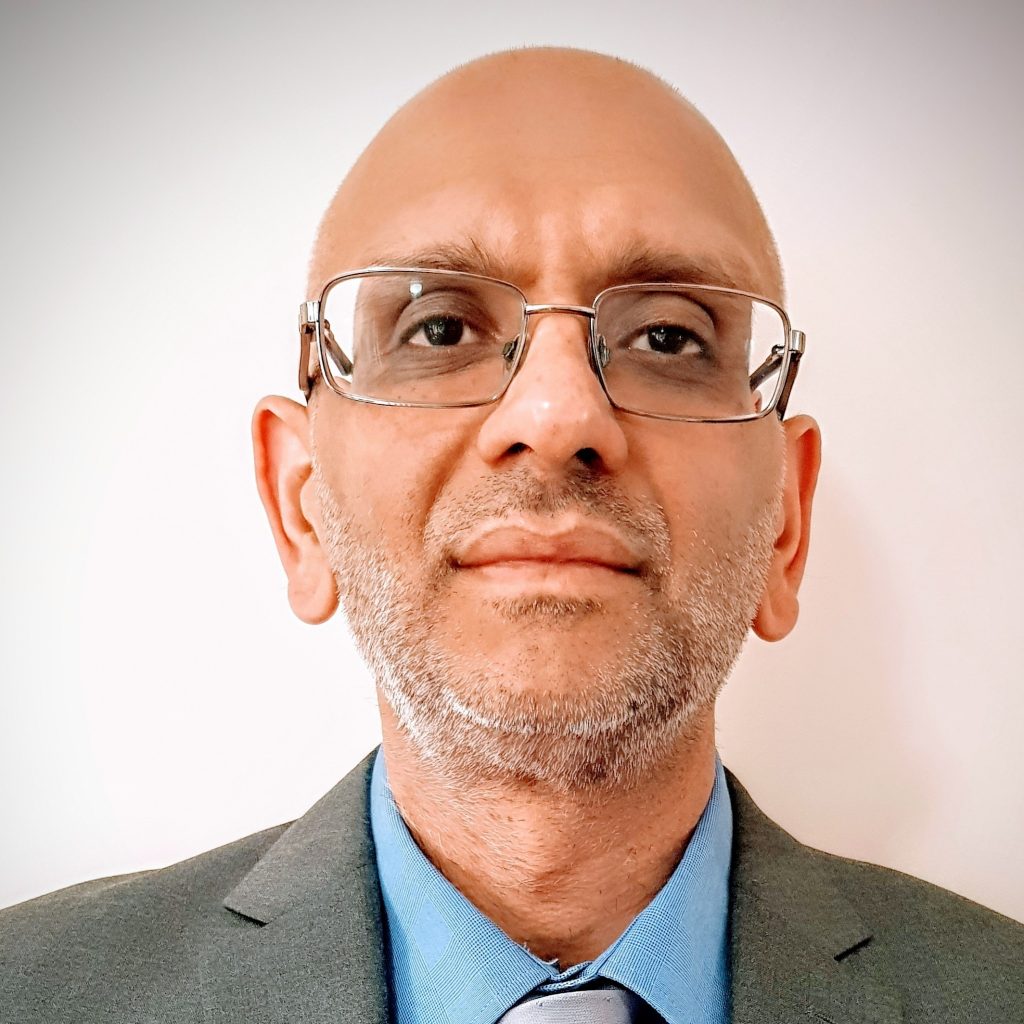
Asif Anwar
Director- Global Automotive Practice
Strategy Analytics
Asif Anwar is a 20-year plus veteran analyst at Strategy Analytics. His current focus is on supporting the automotive industry through the Powertrain, Body, Safety & Chassis (PBCS) Service coverage at Strategy Analytics, providing thought leadership and analysis at the system, semiconductor and sensor levels, as well as looking at the broader whole value chain and tracking emerging opportunities.
Published in Telematics Wire