Alternative Electric Vehicle Technologies
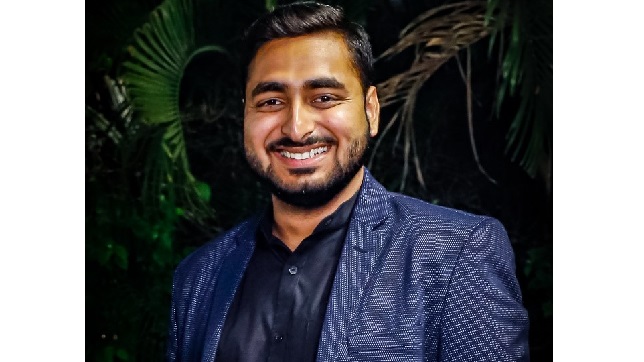
EV scenario in India
The position in which India stands right now needs to have a systematic EV program in place to keep up with the global standards and policies. Potential growth in EV has possibilities for developing a leadership role in this segment. As electrification is the major emerging trend amongst the Auto industries, they have plans for Electric vehicles and their technology.
Before COVID-19, as per Niti Aayog, the EV penetration could reach 80% for two-wheeler and 30% for private cars. If India manages to reach its target by 2030, it could save about 1 Giga tonne of emissions. Looking at the pollution level in major Indian cities, it is the need of the hour.
Post-Lockdown Scenario for Electric Vehicle
Before covid, the Indian auto industry was already in peril to keeping up with the BS-VI emission norms
And it became worse when the complete nation was hit with a lockdown keeping in mind the increasing number of cases and extension of lockdown further added to its woes. Somewhere around chaos, India could seem to be losing its E.V. momentum.
Also, some of the industry leaders indicated that the cost of an Electric vehicle as compared to a conventional vehicle because India is one of the most cost dependent market. Also, the three-wheelers which is a sizable chunk of the electric vehicle segment right now took a major blow because of the concept of social distancing
After this, our Prime Minister started vocal for local initiative and taking a closer look if our businesses are much more dependent on china rather than each other; it would make much sense financially logistically and also will help in future-proofing. Keeping the same in mind I thought of alternative electric vehicle technologies that will diminish our dependencies on china or any other country.
So, let’s start looking at this objectively an Electric Vehicle can be divided into four major Component those are
- Motor
- Battery
- Controller/drive & BMS
- Telemetry System
The last two components are either designed here or assembled here to completely remove dependency from china for these kinds of products we should at least have fabrication unit to manufacture the required ICs.
So, from this point forth our discussion will only be concentrated to moto, batteries and their alternate technologies
MOTOR
Motor for an electric vehicle can be classified into the following categories.
Based on the above classification major market share for an electric vehicle are leaning towards
1. DC Series Motor
These motors are mainly used for traction applications as high starting torque capabilities. Also, the major advantage for these types of motor is comparatively easier speed control techniques, and the ability to withstand sudden increment in load all this makes it an ideal choice for traction application.

But it also comes with a major drawback with these types of motor are the maintenance of carbon brushes as carbon brushes get rubbed against the commutator and are either has to be adjusted or replaced from time to time.
2. BLDC (Brushless DC Motor)
BLDC or Brushless DC motor is called brushless because of the absence of commutator and brush and these motors are inherently maintenance-free. Has high starting torques and good efficiency. They are classified into two categories based on their design.
- HUB Motor
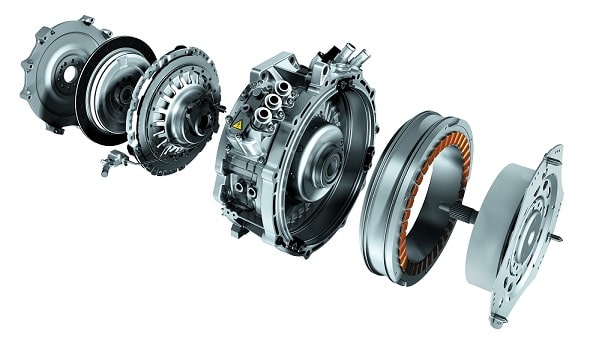
These kinds of motor have a stator on the inner side of the motor and Rotor is on the outer side and the rotor is directly connected to a wheel.
These motors are used for two-wheeler and electric bicycle application due to the following reasons
- As it is directly mounted on the wheel it does not require any external gear system which makes the overall transmission system less bulky.
- Also, it saves mounting space which is a major constraint in two-wheeler and electric bicycle applications.
Due to the above application-specific design, the size is a major constraint in these motors which ultimately translates to a limit in output power.
- Normal BLDC Motor

This motor is like a conventional motor it has a stator on the outside and a rotor on the inside of the motor. It also requires an external transmission to drive the wheel as shown in the image (Ather 450x belt drive transmission system) and differential transmission systems used in E-rickshaws. Due to this, they are a bit on the bulky side when compared to the HUB motor.
Mostly these motors are used in E-rickshaw which is the major part of the electric vehicle market in India and some scooters and bikes whose power requirements exceed that of a HUB motor.
3. PMSM (Permanent Magnet Synchronous Motor)
Permanent magnet synchronous motor is made by embedding permanent magnets in the steel of the rotor to create a constant magnetic field.
Its construction is similar to that of a BLDC motor which also has magnets on the rotor. In this the stator has winding connected to an AC supply and when the current passes thru; it produces a rotating magnetic field.
Now the major technical difference between BLDC and PMSM is the back EMF.
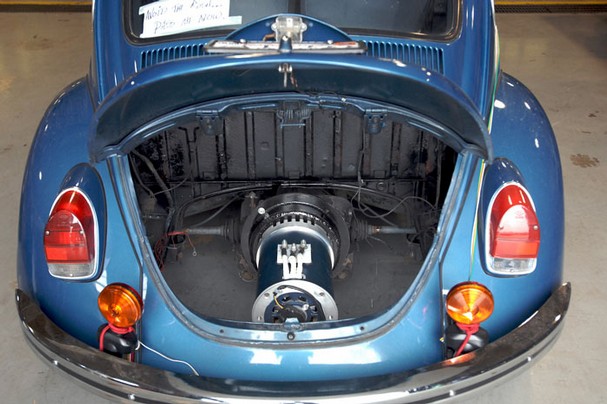
The main advantage of PMSM is that has a higher power density than that of BLDC motor since the motor size is small so it can house more power than its counter BLDC.
But it has some disadvantages to name a few it’s very costly due to high-quality magnets used to maintain and its efficiency and performance. The controlling of these motors is also complex since you can change currently in the stator only and only one power source to play with.
The above motors make up the majority shares in electric vehicle markets and there are some drawbacks and issue with all of the above
- The cost of all of the motors is tremendously high due to the use of high-quality magnets which are made of rare earth metals.
- Also, higher safety measures are required.
- It’s not a permanent or a long-term solution because the strength of magnets reduces over time and also it reduces due to heating in the motor.
- And it creates a dependency on china; as china controls the world supply of rare earth metal (neodymium magnets).
- And this creates an issue if we try to make the motor indigenous we would still be depending on china for magnets.
So, in Alternative technology of motors, we need to choose a motor that less or not dependent on magnets. Keeping that in mind we get the following alternatives
Alternative Technology for Motors
- Induction Motor
When it comes to sheer cost and robustness of a motor induction motor takes the crown it also has a good efficiency which is comparable to that of Permanent Magnet Synchronous motor. Although the induction motor does not have a high starting torque it can be using various control techniques like the field of control (FOC). Induction motors are very low maintenance and have a longer life cycle.
Its major drawback is that that the control circuit is very complex but since this technology is around for so long time there are experienced design houses that can design the required system without any problem.
EV companies like tesla have already shifted towards induction motor to decrease dependency on china.
- SRM (Switched Reluctance Motor)
Switched reluctance motor is robust with a simple construction. Rotors are made up of laminated steel with no winding or permanent magnets on it and the stator is on the outer side. This motor has some advantages like
- due to lack of windings and magnets on the rotor, it makes the inertia independent from the rotor which gives higher acceleration to the motor that is why it is suitable for high-speed applications.
- The power density of this motor is very high which is a major desired characteristic when it comes to bigger vehicles.
- Since the heat generation in the motor is mostly concentrated on the stator part the management of heat is pretty easy
The major drawback with SRM is its complexity is increased as control and switching are increased in this motor. But the companies are considered that and they are developing a dedicated controller in parallel with the motor and selling it as a package.
Battery
All the performance parameter of an electric vehicle solely depends on the motor and the battery. While using a bigger size motor is not a big deal; The issue lies in designing a proper battery pack that provides required amount of current to motor also be able to provide peak current to motor without rapidly degrading the battery life.
The battery is made up of two major components Anode and cathode
The commonly use cathode for electric vehicles is as follows
- LFP (Iron Phosphate)
- LCO (Cobalt Oxide)
- NMC (Nickel Manganese Cobalt)
- NCA (Nickel Cobalt Aluminum)
The major market share of these batteries are lithium ion batteries some are trying to come up with different chemistries.
And major contender is
- Cobalt it has excellent thermal stability property because of which it increases overheating capabilities and results in higher density battery
- Nickel is relatively cheap and has high specific energy
- Aluminum is good conductor
Right now, china holds approximately 70% of the total worlds Lithium ion battery manufacturing capacity
As shown in the graph Chile has the largest lithium reserve followed by Australia and others. Meanwhile Tianqi Lithium, a Chinese company has paid approximately 4 Billion dollars to own second highest share in Sociedad Química y Minera (SQM), a Chilean mining company Which effectively gives china a control over half of worlds lithium reserve
So, in Lithium race china is a step ahead and if we want to remove dependency form china in this matter we need to have a different fuel cell chemistry altogether.
Alternative Battery Technologies
- Super Capacitors
Supercapacitors are energy storage devices that bridge the gap between electrolytic capacitors and rechargeable batteries. Supercapacitors can run for one million cycles compared to 1,500 cycles with existing Lithium-Ion battery technology.
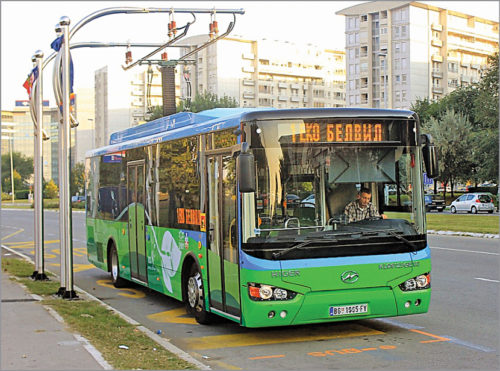
A capacitor vehicle, as shown in the image, is a traction vehicle that uses supercapacitors to store electricity. In general, supercapacitors can store about 5 per cent of the energy that lithium-ion rechargeable batteries can. This limitation restricts the range of driving to a couple of kms per charge. But they can be charged in a matter of seconds. So, in public transport systems such as buses that have to stop frequently at known points where charging facilities are installed, using supercapacitor as the energy storage device is quite viable.
- Aluminum fuel cells
Aluminum fuel cells are basically made up of 3 components water, aluminum and carbon (Graphene). In this they have aluminum cassette in the middle
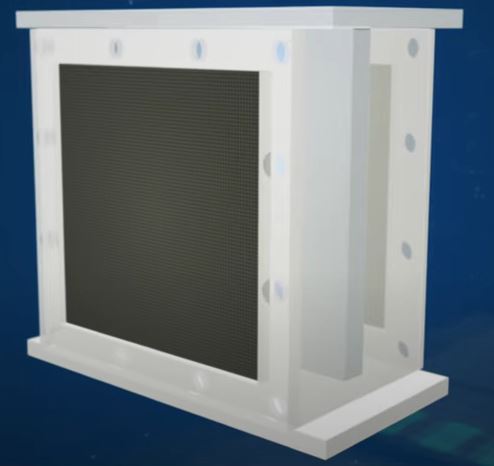
And two graphene membrane on either side this membrane filters carbon dioxide and lets oxygen in when energy generation is required water flows into the chamber and mixes with oxygen and covert aluminum to aluminum oxide which in returns generate energy to power vehicle.
The major advantages in this technology is
- The raw material for the cells is much easier to obtain and it is in abundance so the manufacturing cost will be considerably lower than that of lithium ion batteries.
- The aluminum plates are recyclable once exhausted can be turned into oxidized powder and then aluminum can be reobtained thru it.
- There is no harmful emission.
- No charging is required instead you have to change aluminum plates that can be done in minutes.
- The energy/Kg is 7 to 8 times as compared to Lithium ion batteries.
Conclusion for Alternative technology
The electric vehicle motor selection is pretty tricky to the required or desired vehicle performance has to be known. Also, as far as low-cost and low-speed two-wheeler and three-wheeler are concerned it will be no brainer to use BLDC or HUB motor. But as we move towards the higher power & high performing two-wheeler, commercial as well as private vehicle the clearer choice right now is PMSM or Induction motor but as the production of Switch reluctance motors are made cost-effective as PMSM or Induction motor than one will have more options to choose for electric vehicle application
In my view for want mass EV adoption we are still dependent on china mainly for lithium ion batteries and this will result in increase of already growing trade deficient with china.
Author:
Shubham is an Electrical and Electronics Engineer, working as an R&D engineer, handling various capacitor compliance. He also oversees various diversification project and development with keen focus on light electric vehicle technologies to make that last mile connectivity possible.
Published in Telematics Wire