AI At The Edge
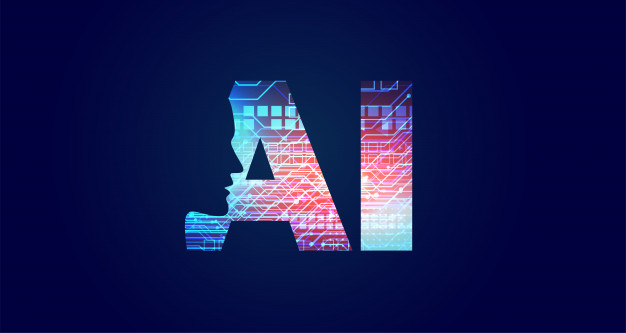
Edge computing is steadily gaining ground in the automotive industry. To carry out complex functions at the ‘localized’ controller is becoming a core strategy for future tech builders. This, instead of sending all raw data to the cloud where all the corresponding analytics algorithms are deployed. As requirements transcend traditional telematics and analytics providers break new ground, widespread edge computing is inevitable. As these evolve so will the need for AI, to the point that Reactive AI may see a rapid move to Limited Memory AI.
This does not mean the edge should do all the functions. Rather, it be entrusted with the vital instantaneous processes and strategic ‘heavy lifting’. Functions carried out in the cloud may be serving other purposes which don’t need real time priority. Both edge-processed data and strategic raw data will be beamed to the cloud. So what kind of real time functions would new telematics ecosystems handle such that edge computing be so vital to them, you may ask. Prognostics or preventive maintenance at the edge has great potential to cap emissions. How this can be achieved needs a quick explanation of the difference between diagnostics and prognostics. The powertrain Engine Control Unit (ECU) irrespective of its motor windings or pistons has a tried and tested diagnostics software layer built for sensing and reporting all kinds of failures. What this layer does not possess is the ability to sense interim deterioration and quite often a partial failure. This deficiency can be made up with raw data analytics. The prognostics layer is a stand-alone layer which can be deployed in the OEM’s Telematics Control Unit (TCU) or even an Aftermarket Control Area Network (CAN) enabled IOT device. The ability to analyze powertrain raw data when the vehicle is operating in the real world is profound. This can happen only at the edge. While this is technically feasible at the cloud as well, sending all this high frequency raw data to the cloud can prove inefficient predominantly because it may become an expensive proposition. Sensing system or sub-system level deterioration via powertrain raw data analytics at the edge can cap tail-pipe emissions for an Internal Combustion Engine (ICE) equipped vehicle. Similarly analytics at the edge for an Electric Vehicle (EV) can forewarn for anomalies in the electric powertrain or degradation of the battery.
AI at the edge is the key to building robust capability to detect underperformance. The application of this is immense. While sensor plausibility checks for the wide array of sensors onboard an autonomous car are no doubt part of its architecture, a holistic system deterioration sensing capability is an imminent addition. The Limited Memory AI entrusted with the safe operation of an autonomous vehicle is perhaps also best employed for this addition. As for the prognostics for the ICE a Reactive AI fused with a domain specific expert system is, perhaps, optimum. This is so because the Aftermarket has a great number of different types of vehicles rendering even the best of AIs, though bristling with learnt patterns and trends, a bit overwhelmed. This strategy can also be used by OEMs when focusing on a particular model being rolled out. It is difficult to say if for this application the hybrid AI will be a good fit or would Limited Memory AI be a better one. Perhaps the latter may be a bit of an overkill, especially when aiming for optimality, only time will tell. The expanse of powertrain engineering widens with every passing year. From internal combustion to battery powered electric to hydrogen electric powertrains, the innovation is inspirational. If we were to focus on just the ICE, the improvements being made are astonishing. The never-say-die attitude of the ICE community is admirable. How else would one explain the lust to challenge the very essence of the ICE – its thermodynamics, or ever evolving forced induction systems, or the artful amalgamation of the ‘i’ and the ‘e’ motors. From Camless engines to fundamental changes in the combustion chamber to the very construction of the century old reciprocating mechanism, the list goes on. Therefore, a watchful hybrid AI makes a good case for itself.
Edge computing can be an important contributor to the complex OEM ecosystem. AI at the edge for real world and real time prototype vehicle testing brings vehicle, tester & engineer closer together like never before. Complicated but versatile software libraries sitting in the edge can compute real time parameters related to engine driveability, performance and emission. The processed data essential for the engineer back at the R&D base is transmitted real time. Edge deployed algorithms watching powertrain health, driver/rider inputs, temperature-pressure gradients of the exhaust gas treatment (EGT) system will inform real time of tester attributes and system underperformance leaving very little raw data for the engineer to deal with. Striving for this seamless and flawless performance from a telematics system is achievable with AI at the edge. Vehicle quality assessment at the End-Of-Line (EOL) is another area for AI based edge computing. Also an Industry 4.0 application, this is an interesting potential starting point for edge computing at the beginning of the automotive value chain. Whether its vehicle testing at the EOL chassis dynamometer or track testing, both will use an AI powered small footprint computing unit. The unit with real time visualization will guide the tester with instructions for perfectly choreographed data mining so as to feed the AI for a step by step assessment and result declaration at the edge. The results against each Vehicle Identification Number (VIN) are sent from the edge to the OEM’s cloud for archiving. This digital detailed powertrain health record would bring unprecedented quality control and management ensuring every vehicle leaving the factory is as perfect as the other. A variant of this solution for the OEM dealership adapted for a typical urban test drive in lieu of the regimented EOL one for powertrain health assessment would truly connect the two ends of the spectrum. This ability to track the vehicle from its place of birth to its place of upkeep can be of great value to the OEM in more ways than one. It would provide incessant accurate data for superior vehicle design & engineering, reduced warranty claims, customer delight etc. With emission legislation mandated feedback and confirmation of performance proofs required by the authorities this capability can prove very utilitarian for all involved. There is also the ever attractive cost reduction factor which could make a strong point for OEMs looking to reduce expenditure on expensive vehicle mounted Portable Emissions Measurement Systems (PEMS). These, ofcourse, are the gold standard of real world emission measuring systems but may not be needed for all tests. AI powered CAN enabled IOT devices running complex algorithms to monitor and accurately predict EGT real world performance and premature failures are becoming a reality. Wayward Diesel Particulate Filters (DPFs), Lean NOx Traps (LNTs) and Selective Catalytic Reductions (SCRs) could be checked both at the EOL or monitored during prototype vehicle testing.
Introducing AI at the edge for real time decision making is the natural next step of distributed analytics. There is no doubt that AI at the edge is a game changer. To automotive professionals from various fields this opens up new frontiers. The future is optimum.
Author:
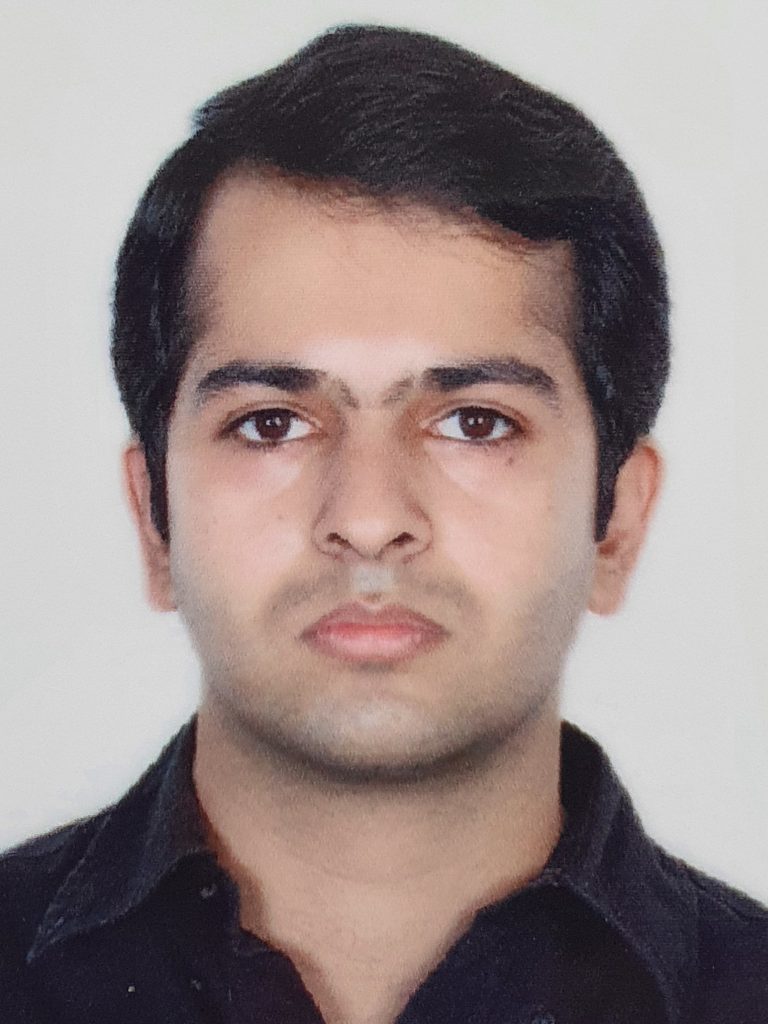
Anubhav Amarnath
CEO
EngineCAL
Anubhav Amarnath is a passionate automotive engineer. He claims he has been lucky to work in areas of powertrain engineering which have truly broadened his thinking and instill ideas. He is grateful to his former employers and colleagues for the prolific work he was made part of. He works as the CEO of EngineCAL.
Published in Telematics Wire