Building Vehicle Health Management Functions with SAE JA6268 Methodology
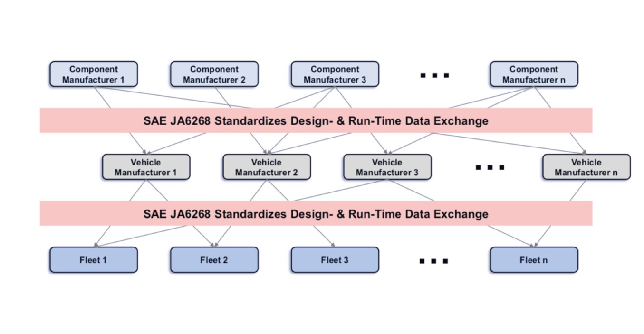
Background
IVHM (integrated health management) systems are ushering in a new paradigm for diagnosis and prognosis with the concept of “ Health Ready Component”
Presently, the vehicle systems are primarily operating in the diagnosis-only paradigm where the focus was to facilitate the detection and identification of the root cause(s) once a failure had occurred. This has found limitations in effective diagnostics resulting in No Trouble Found (NTF) cases adding to warranty cost and customer dissatisfaction. It is imperative to enhance the diagnostics coverage and support prognosis, to facilitate health monitoring and tracking of system degradation severity to prevent a given component from degrading to the point where it goes outside its operational performance envelope. This is possible with the big data cloud computing, predictive analytics, and Advanced telematics for Connected Vehicles.
There are barriers to implement this and mainly contributed by
- Multiple players: T1, T2, OEM, operators, individual owners and users
- Evolving vehicle architectures
- Multiple variants with potential low volume
- High variation of diagnostic and service procedures
- High variation in technician skills
- OEM customisation beyond standard
- Lack of uniformed signals, nomenclature
The figure 1 shows how the interoperability among the IVHM functions are hampered by differences in data exchange among the stakeholders.
The SAE JA6268 specification from HRCS consortium addresses existing barriers to the successful implementation of IVHM technology for the automotive, commercial, and military vehicle sectors. Original Equipment Manufacturers (OEMs) in all these sectors are heavily dependent upon a large number of component and system suppliers, many of which are shared across these sectors.
The advent of IVHM technology has accentuated the need for a new model that encourages better coordination and communication between the OEM and its suppliers in order to achieve the operational, safety and economic benefits desired.
SAE JA 6268 seeks to provide uniform requirements, practices, and methods to address the sharing of critical component/subsystem run-time messages and supporting design-time information to facilitate real-time platform level communication and implementation of the supplemental IVHM functions.
IVHM Process with SAE JA6268
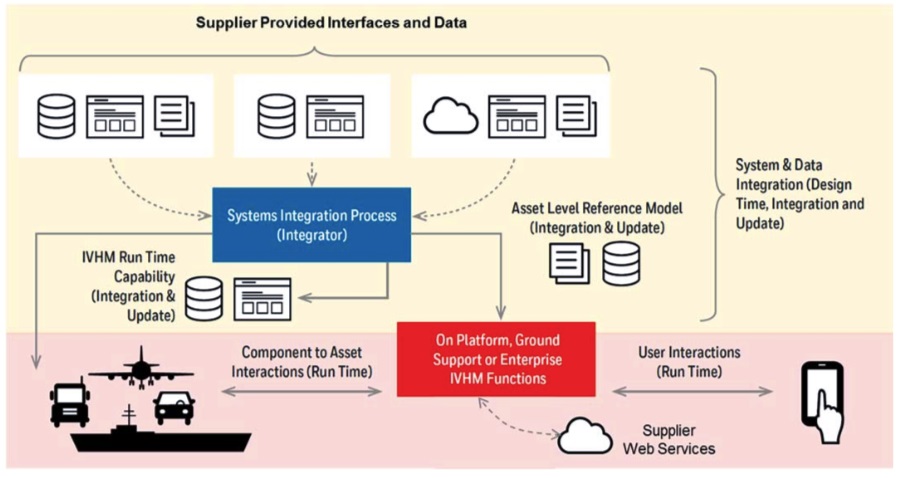
IVHM Process from the figure 2 shows,
- The design and data integration process
- The integration of IVHM related run- time messages. Design-time integration uses data developed by suppliers and provided to the system integrator (highlighted in light beige ) in order to provide more complete implementation of IVHM functionality and to facilitate the integration of this functionality.
- Run-time messages are collected by the Health Management System(red block ) and used by higher level reasoning functions to provide the best possible component health state advisories and support services to the various user communities
Benefits using SAE JA6268 Methodology
- Engineering Cost Saving – Reduce the effort to develop high accurate diagnostics functions and health indicators
- Improve diagnostics coverage, reduce diagnostics ambiguities leading to reduction in No Trouble Found (NTF) rates and reduction in diagnostics time
Evolving Industry Capabilities – Moving from Cloud based Monitoring to Vehicle Health Management
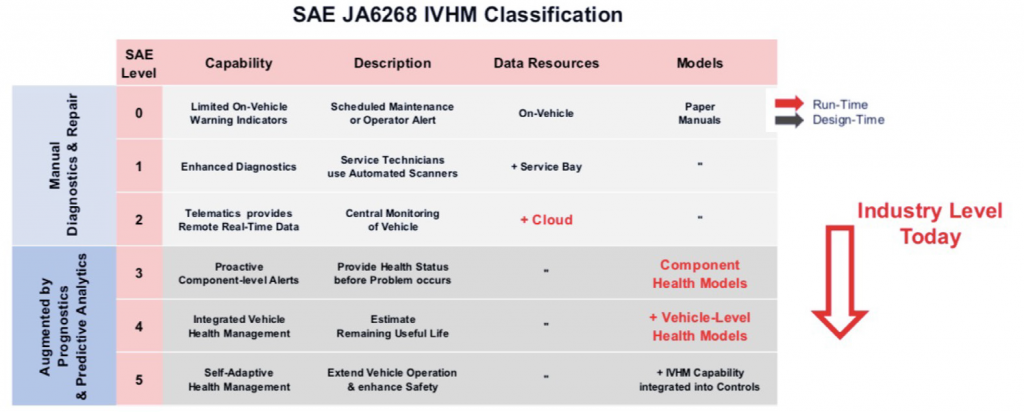
Figure 3 shows the industry defined IVHM classification levels and the way the industry is moving to adapt this. Current Level 3 and 4 are what the industry is targeting.
- Implementing IVHM functions using SAE6268 methodology
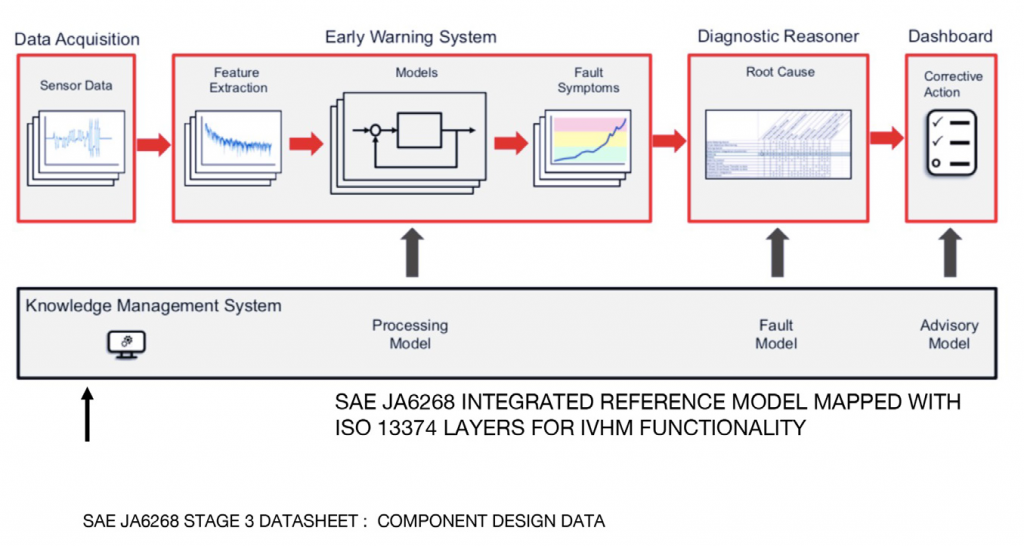
The information provided by the design-time data submittals as SAE JA6268 data sheet is used to build an IVHM Integrated Reference Model (IRM) as shown in the figure 4,.This consists of a Fault Model, a Processing Model and an Advisory Model . The design data integrated with ISO 13374 layers to develop run-time processing and analysis to assess health, estimate time to failure and determine the root cause for fault..
1.The Fault Model specifies the characteristics of the functional failure modes of the component, the inputs and their effects on the outputs and symptoms of the component.
2.The Processing Model specifies the dynamic models between Input/Output (I/O) variables and specifications for data collection, data trending and algorithms to generate additional diagnostic and prognostic indicators as well as algorithms to generate prognostic estimates of “time to fail”, i.e., remaining useful life.
3.The Advisory Model contains the information needed to interact with the user and the command system functions as required to isolate and correct any detected faults. Content of the Advisory Model includes links to repair procedures, manual test procedures, initiated test procedures and links to Option Codes to allow a single model to encode effectivity of entities based on versions and variants of the component, system, or platform.
IVHM ISO 13374 Function Blocks
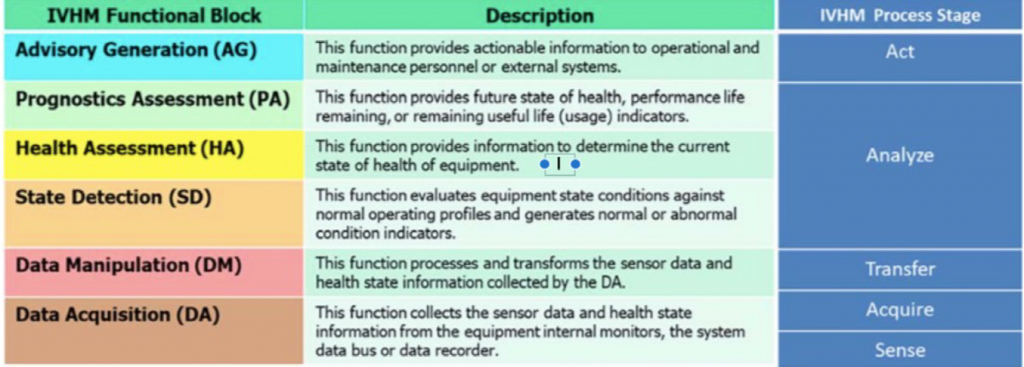
As in Figure 5 , DA is the lowest level block and acquires sensor output data. The next level, DM implements low-level signal processing of raw measurements from the DA block. The SD level supports modelling of normal operation and detection of operational abnormalities and creates a CI (Condition Indicator). A subsystem can generate multiple CIs depending on the number of sensors. The CIs are communicated to the next level, HA where the health of the system is established by creating a HI (Health Indicator) . Depending on the type of subsystem and the complexity of interaction with other subsystems, HA might be performed at the subsystem or vehicle level.
The upper three functional blocks of the model provide decision support to operations and maintenance personnel based on the health of the target system. Within this group, the HA function provides fault diagnostics and health condition assessment. The PA level is aimed at enabling the forecasting of future health conditions based on current state, projected usage and the operational envelope.
It is required to build reference model for IVHM using design data and map it to ISO 13374 function blocks.. For this, it is required to perform systems engineering analysis at the system, subsystem or component level to characterize their inherent IVHM capabilities. For existing components, these will typically consist of functions addressing the foundational layers of the model (DA, DM and SD) but in some cases, will also include the higher-level functions (HA, PA and AG). All areas where the existing implementation does not provide the required functions should be identified.
Runtime Data Processing of JA6268 Component ( Smart Pump Example)
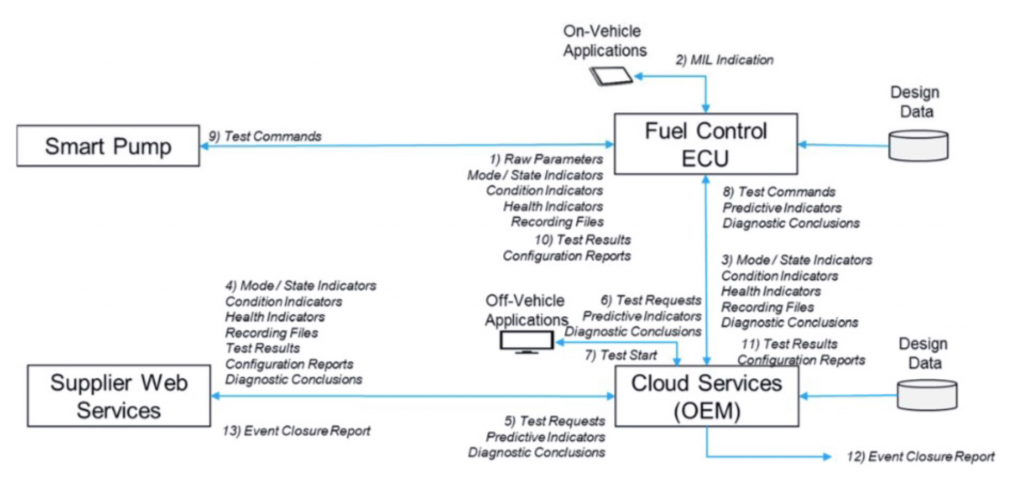
Figure 6 shows the standard example of run time message data exchange between Health Ready Component(Smart Pump), ECU, OEM Cloud Services, Supplier Webservices.
Here Smart pump is a digital twin implementation of the pump by the component supplier using design data. The twin monitors the pump behaviour periodically logging the data
exchanged with ECU and provides health indicators and root cause information. The OEM can use this information to provide cloud services for reporting trending of health indicators at vehicle and fleet level with recommended actions.
When there is ambiguity of diagnostic conclusion, data can be sent to supplier who will investigate the diagnostics conclusion with design data and update the diagnostics, predictive indicators and test methods
To resolve the ambiguity via the web services to OEM cloud service which will inform the maintainer or service technician,
To use the information provided supplier to test and update the cloud services of the fix and close the issue.
- JA6268 templates and data sheets
SAE HRCS is developing Templates for Stage 3 to Reduce Effort, Improve Accuracy and Ensure Interoperability. The stage 3 template is for component design data submittals. Only the common signals are shared while the proprietary signal and the design data is shared by the supplier with OEM.. Figure 7 shows the template information provided by SAE JA6268.
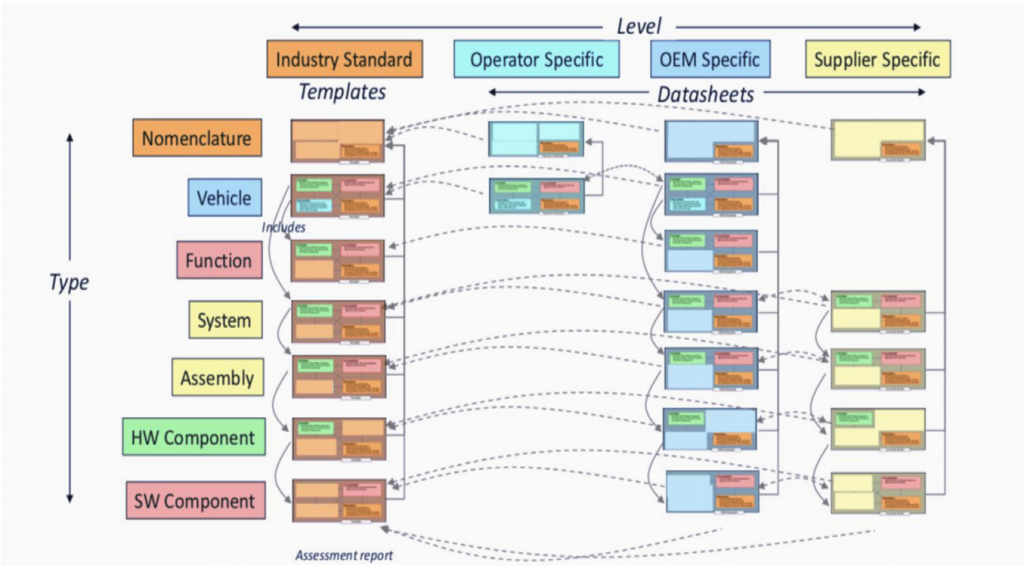
SAE JA6268 VHM Functions Development ToolChain
- There are companies who have developed toolchain for developing Health indicators from JA628 data sheets for Advanced Diagnostics and Prognostics. The tool integrates Design Time and Run-Time Data to Greatly Reduce the Cost to Deploy Predictive Maintenance Solutions.
- IntelliPredikt has come up with such a tool that enables development of VHM using run time and design data for the cost effective development of VHM functions.
- Use case of using SAEJA6268 for commercial Trucking pilot and result
This provides a uses case of our partner company DG Technologies who participated in the Commercial Trucking Phase 1 Pilot program with SEFL trucks with SAE / ATC. Setup is shown in figure 8.
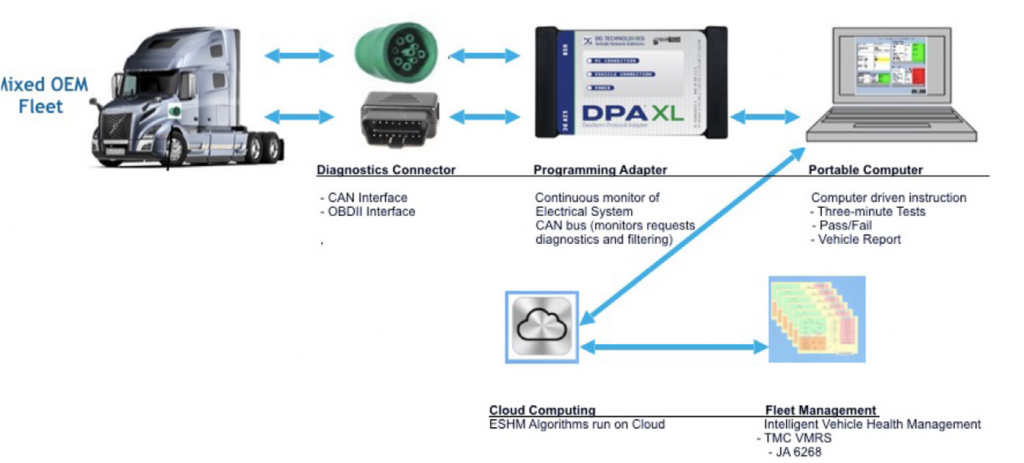
- They Demonstrated validating JA628 generated health indicators and diagnostics time reduction for Truck Electrical Starting System
- Used JA6268 stage 3 data sheets to create Fault models and produce health indicators.
- Demonstrated interoperability with Mixed OEM Vehicles in fleet
Below shows the process followed as shown in Figure 9.
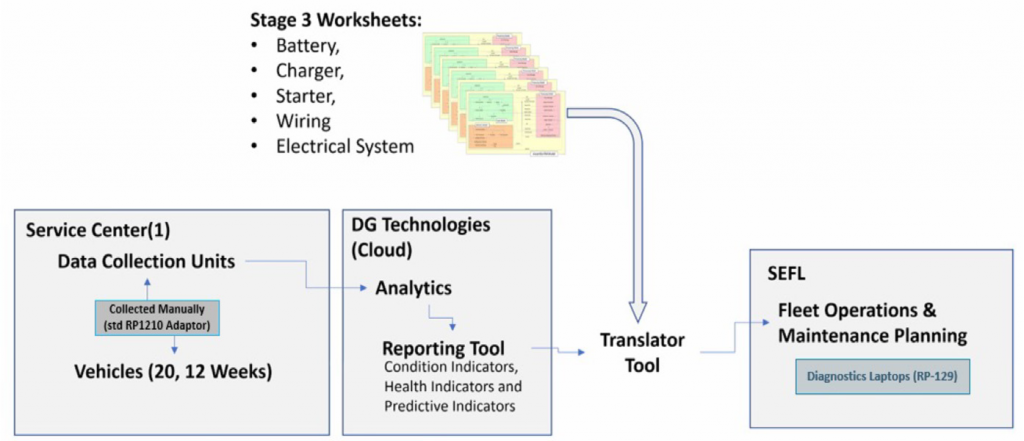
- Results
Figure 10 shows the results obtained from JA6268 Phase1 Pilot
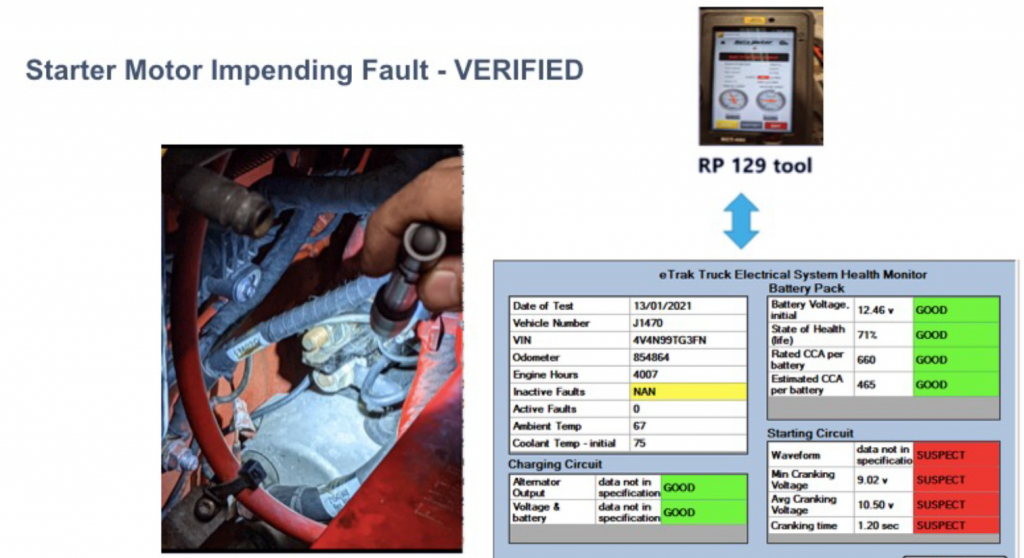
- Efficiency gain:
- RP129 maintenance procedure is 45 minutes
- Pilot project demonstrated a system test time of less than 3 minutes to isolate path to hard failure
- Identified an opportunity to reduce regularly scheduled maintenance (ONLY when conditions warrant)
- Provide an off-board diagnostic solution of the primary electrical system
- Battery, starter, alternator and cable) through the diagnostic connector
- Utilise JA6268 Stage 3 Data sheet / signal mappings to develop a non-intrusive systems test
Author
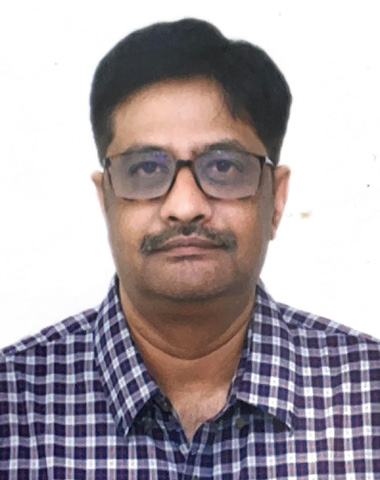
BK RAMESH
Director of AI – Predictive Health Management and Control
IntelliPredikt Technologies
BK Ramesh is Co-Founder and Director of AI for Predictive Health Management & Control. At IntelliPredikt Technologies he is actively involved in implementing AI applications and business strategies for IntelliPredikt and closely working with Global research universities, Data Scientists and Consortiums, Partners ecosystem, and Customers which include OEMs and Tier1 suppliers.
Published in Telematics Wire