Powertrain Informational ADAS
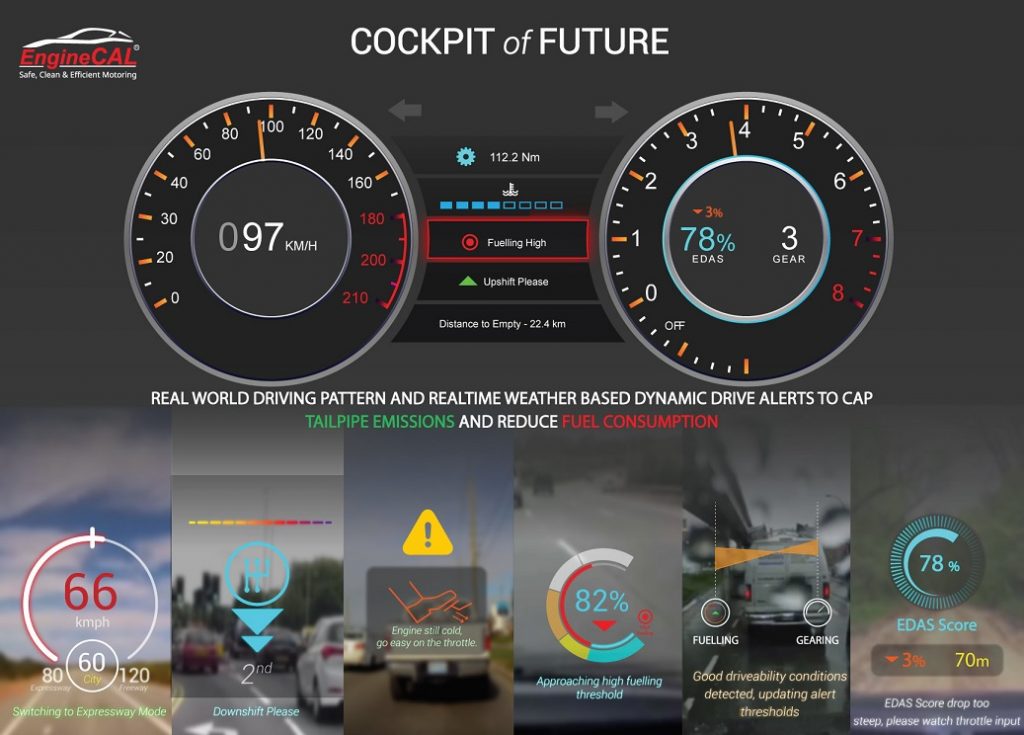
Think tanks and future mobility reports have predicted an emergence of vehicle energy smart management. A broad area of technology, no doubt, enveloping the powertrain. One of the many contributors to this is realtime vehicle energy demand. This tech layer could become the future brain of the powertrain management system regardless of its internals being pistons or motor windings. Its more probable that the EV may receive the TLT – tender love and tech. So what is this got to do with ADAS?
ADAS could be one medium to optimum driver demand. Driver demand is the tech layer of the engine management system responsible for taking commands from it’s human for desired motive power. Realtime advice in the form of an instrument cluster indication for a select band of throttle usage has been prevalent in passenger cars and 2-wheelers. But intelligent engine performance control, one which is variable and hence optimum is a step above these now legacy systems. Ofcourse, such a system will need to be connected. It would seamlessly become a part of the vehicle’s network being fed realtime weather conditions, road specific traffic information etc. over and above the all-important powertrain CAN data. Why weather conditions you may ask. In order to provide precise and accurate driver demand inputs to the human the tech must be aware of the ambient conditions. These have direct implications on driveability. It all boils down to, pardon the pun, the combustion. The right conditions aid better cylinder filling resulting in better combustion and therefore, more performance at the flywheel. All this as an intriguing form of ADAS – powertrain informational ADAS.
The slightest of factors affecting driveability need to be part of the software layer realtime ingesting his/her inputs, calculating an optimal demand and relaying to the driver. This demand layer has to be powertrain specific and designed around the target powertrain’s driveability calibration. The audio and visual cue for approaching the optimum driver input and for breaching it can be projected on the HUD, the cluster or even the infotainment system. The optimum demand is not a signal to continuously follow and so will remain dormant but watching it’s human. Once the driver is close to breaching the current optimal demand the system will signal the driver to adjust throttle which could be both hold or reduce. The signal will be different if there is a breach. Tests have shown that humans can adapt to such a system bringing in remarkable change in drive patterns. Drive patterns which see per drive cycle superior CO2, safety, less stress on the powertrain, the list goes on. While globally the Real Driving Emissions (RDE) is one way to ensure real-world drive patterns see closer results to the vehicle laboratory emissions, RDE still works with conformity factors. Further, RDE is for select components of emissions. These, ofcourse, are agreed standards by the global automotive emission legislations. The point being made here is that any additional tech to achieve an improvement in realworld tail-pipe emissions is going to be helpful. A special ADAS of this genre could complement the brilliant work of the men and women in this field. A more controlled, subtly ofcourse, drive pattern will impact the realworld tail-pipe emissions performance.
This intriguing version of ADAS will also have certain benefits similar to current ADAS applications. In other words, safety of the occupants and of the vehicle. In-cabin feel is enhanced when driver demand is optimum. While this sounds more a comfort enhancement it is in fact more wholesome than that. This automatically reduces the possibility of near-misses or even accidents with an optimum rate of acceleration. The safety enhancement applies to the powertrain too. Optimum driver demand can be, in the long run, a method to extend component level life because of capping harsh use. There is another perspective to this. Monitoring drives such that realtime alerts advice the human not to shut off the engine before operating temperatures are reached. Or, not to push the powertrain because it is still cold. Maybe even, not abruptly shut down the engine after a hot run. Such alerts will simultaneously impact emissions, protect the forced induction system, engine oil etc.. Often drivers subconsciously follow a harsh driving pattern little realizing that their ‘innocuous’ drive could be far more optimum, and safe.
It must be clarified that optimum driver demand for vehicles equipped with manual transmission include gear management as part of the alerts engine. This too has been seen for long in the passenger car segment. And again, this can be improved on by considering weather conditions and certain strategic realtime powertrain CAN information as part of this informational ADAS. Gear management is a deep topic in itself. Typical driver usage is low engine speed, high gear. Often, the reason for this driver strategy is the insatiable quest for a better fuel figure and sometimes lethargy. While the latter is more tongue in cheek there is no doubt that the former is widespread. Unfortunately this gets sometimes stretched which keeps the powertrain operating at high loads low revolutions and the typical urban traffic conditions don’t help either. This leads to more soot accumulation in the diesel catalytic convertor, DPFs and GPFs. The repercussions of this is well understood. If there is anything as ‘holistic deterioration’, this is it. An underperforming catalyst to poor engine performance, it goes on. Though this article is not about the exhaust gas treatment (EGT) system it wont hurt to say that the aforesaid lines do pose a lot of trouble for the systems running particulate filters. DPF equipped vehicles running in congested megacities face issues with engine oil dilution and choked DPFs. As seamless as the regeneration process was designed to be, the human not knowing about an ongoing on regeneration poses some problems. If an engine shut off is initiated by the driver while regeneration is active, the process of clearing out the DPF gets stretched. It spills into the next drive cycle and maybe another all while more soot is being continuously accumulated. This can happen in the urban jungle often resulting in a scenario where the DPF needs the service center’s intervention. Powertrain informational ADAS could learn/track and decide which drive cycle to advice it’s human to allow the regeneration to be completed.
Connecting the vehicle’s prognostics technology to this ADAS will be necessary. Prognostics beats the on-board diagnostics layer in detecting deterioration and can predict failures. A link with the vehicle’s prognostics tech will be vital realtime information for optimum driver demand. A drop in engine performance will require an intelligent algorithm to be embedded in the optimum driver demand decision engine to calculate any leeway, if at all. This also means state of the art prognostics capability to assess various systems like injection, ignition, forced induction etc. If any exhibit deterioration it will impact engine torque, a parameter which new generation prognostics layers are able to calculate based on powertrain specific AI models.
Automotive technology has been incessantly evolving. We ‘humans’ are in the golden era of advanced, utilitarian and delightfully ‘assistive’ cockpit electronics. The future is optimum.
Author:
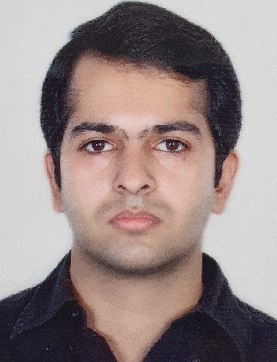
Anubhav Amarnath is a passionate automotive engineer. He claims he has been lucky to work in areas of powertrain engineering which have truly broadened his thinking and instill ideas. He is grateful to his former employers and colleagues for the prolific work he was made part of. He works as the CEO of EngineCAL.
Published in Telematics Wire