Volkswagen Group commences climate-friendly MEB production at Foshan and Anting plants
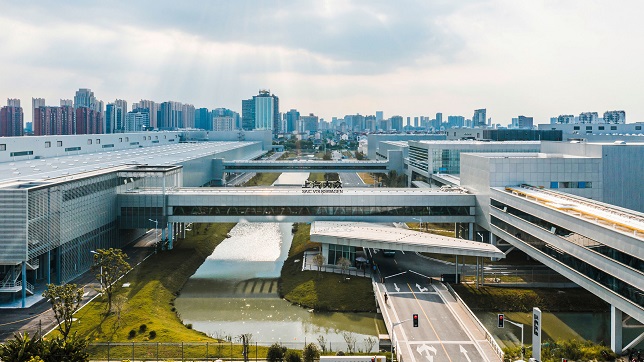
Volkswagen Group has entered a new era of e-mobility in China with the premiere just three weeks ago of the first two China-specific models from the completely new, electric-only ID. family – FAW-Volkswagen’s ID.4 CROZZ01 and SAIC VOLKSWAGEN’s ID.4 X01 – built on the innovative MEB platform. With market entry in early 2021, production of these two models has already started at MEB facilities in Foshan and Anting, which together have a combined total planned annual capacity of 600,000 units. This will enable the Group to increase the share of electric vehicles in its product portfolio to 35% by 2025. By 2023, Volkswagen will offer eight models of the ID. Family in China, the world’s largest NEV market which plays a crucial role in the Group’s global e-mobility strategy.
“Our ID. family, based on the MEB platform, will be an industry game-changer and will revolutionize the NEV market. The MEB provides unique versatility and is an incredibly flexible platform for vehicle production, meaning, we can offer customers a wide range ofhighly attractive electric models, from compact city cars to spacious buses or SUVs,” said Dr. Stephan Wöllenstein, CEO of Volkswagen Group China. “The start of production at the first two MEB plants in China is a true milestone and will take our e-mobility push mainstream, making quality NEVs affordable for many people.”
Standardization for efficient ramp-up
The Anting MEB plant is Volkswagen Group’s first greenfield MEB plant anywhere in the world, 100% dedicated to the manufacture of pure-electric vehicles. Through standardization measures, the infrastructure investment at the new Anting plant was cut by 5 percent compared to previous car plants, despite significant higher costs for site-specific requirements.
The Foshan plant was revamped on the site of original production facilities as one of the most flexible plants in the global production network. It allows to produce both convention ICE models based on the MQB platform and pure-electric models based on the MEB platform on the same production line. A highly flexible set-up enables co-production of 6 to 8 MEB products. With more than 1,200 robots in the welding workshop and an automation rate of nearly 100 percent in the paint shop, Foshan is one of the most productive plants in China.
Both projects were started in the second half of 2018 and fully completed to the point of series production within just two years.
Benchmark for climate-friendly vehicle production in China
The Anting plant implemented 28 energy-saving and eco-friendly measures, including solar photovoltaic power generation, improved heat-exchange systems, intelligent light controls and waste management, as well as rainwater recycling. As a result, energy use, water use, carbon dioxide waste, volatile organic compounds (VOCs) and general waste have each been reduced by 20 percent compared to other vehicle plants of a similar size.
At Foshan, all MEB vehicles will be produced with renewable energy, making the production process CO2-neutral. Furthermore, 200,000 square meters of solar panels have been installed to provide the factory with a power of 8.2 MW and an overall production of 9,000 MWh per year of renewable energy. This leads to a CO2-saving of 7,900 tons per year.Through a water recycling system, 44 percent of the water used in the production process is recycled. Since 2018, the Foshan factory has received 9 national environmental awards for green and energy-saving production methods.